新能源用鈦絲涵蓋純鈦及鈦合金材質。純鈦絲以 TA1、TA2 為代表,TA1 純度高、雜質少,TA2 強度稍高;鈦合金絲中,TC4(Ti-6Al-4V)最為常見,鋁、釩元素的添加優化了其耐熱性、強度與韌性。在物理性能方面,鈦絲密度約 4.54g/cm3,利于設備輕量化,熔點高達 1942K,熱膨脹系數小,能在不同溫度環境下保持尺寸穩定。機械性能上,鈦絲強度高、韌性好,具備出色的疲勞性能,可承受長期循環載荷。耐腐蝕性能是其突出優勢,表面形成的致密氧化膜,使其在海水、氯化物、酸堿氣體等惡劣環境下,遠超鋼絲和不銹鋼絲的耐腐蝕能力。國際上,中美及國際標準均對鈦絲牌號有對應規定,如中國 TA1 對應美國 UNS R50250,便于全球產業協同。
鈦絲加工需注意多方面要點。刀具應選用硬質合金或金剛石材質,加工速度需控制在較低水平,以避免因發熱影響性能與加劇刀具磨損;同時要防止與鐵、碳鋼接觸,避免表面污染。常見產品規格直徑范圍在 0.1mm - 6.0mm,長度可達數百米,形態包括鈦盤絲、鈦直絲等,可滿足不同生產需求。在核心應用領域,鈦絲已廣泛應用于風力發電與太陽能發電。如在風力發電塔架纜繩、葉片主梁結構中,憑借高強度、耐腐蝕和輕量化優勢,提升塔架穩定性與使用壽命;在太陽能光伏支架系統及聚光太陽能發電設備中,用于部件連接與結構支撐,確保長期戶外使用性能穩定。
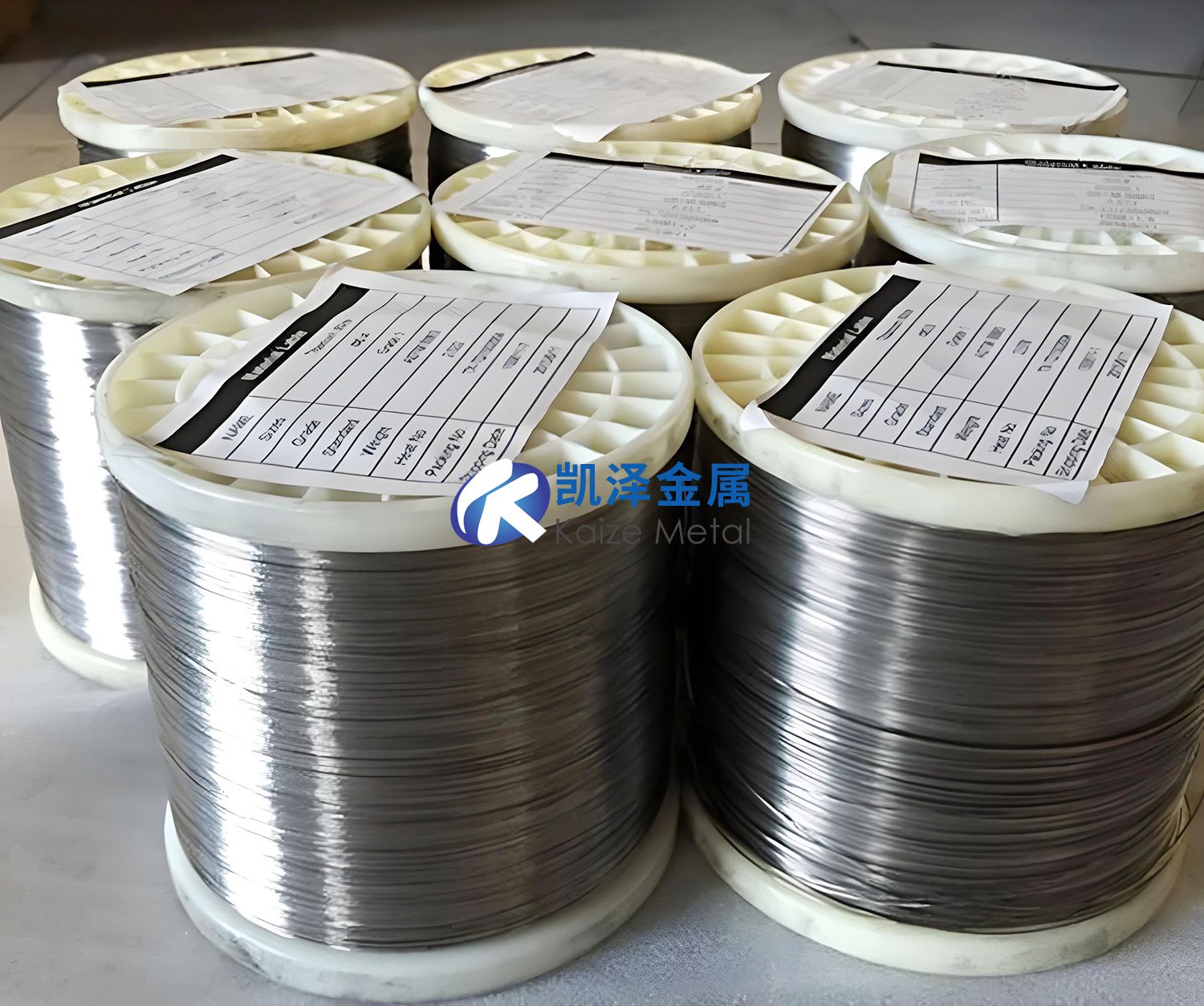
鈦絲制造工藝復雜且嚴謹。熔煉環節通常采用真空自耗電弧爐,保證成分均勻、減少雜質;熱加工在 β 相區鍛造后進行軋制或擠壓成型;冷加工通過多道次冷拉拔結合中間退火,控制尺寸精度與性能;表面處理采用酸洗、陽極氧化等方式,提升耐蝕性和耐磨性。以 TC4 鈦合金絲為例,其工藝流程涵蓋原料準備、熔煉、鍛造、熱軋、酸洗、冷拉拔、表面處理、成品檢驗直至包裝入庫。執行標準方面,國內遵循 GB/T 3623 - 2007 等,國際上參照 ASTM B348、AMS 4928 等,醫用鈦絲還需符合特定醫療認證標準,確保產品質量與性能的一致性和可靠性。
在新能源用鈦絲產業發展上,國內外呈現不同態勢。國外歐美國家起步早,技術先進,高端產品在航空航天等新能源相關設備應用成熟;我國近年來雖規模不斷擴大,但在高端產品研發生產上仍與國外存在差距,部分高性能鈦絲依賴進口。先進制造工藝的進展為產業帶來新機遇,增材制造實現復雜形狀部件的高效生產,精密加工滿足高精度需求。當前技術挑戰主要集中在提高生產效率、降低成本以及研發高性能鈦合金。未來,隨著海上風電、分布式太陽能發電等領域發展,鈦絲需求將持續增長,技術創新與綠色環保生產將成為重要趨勢,推動鈦絲在新能源領域應用范圍進一步拓寬 。凱澤金屬基于氫能光伏及儲能領域用鈦絲的技術、材料性能、產業布局,結合最新科研成果,將其整理如下:
1. 核心應用場景與技術參數
應用領域 | 功能需求 | 鈦絲規格 | 性能優勢 |
氫燃料電池雙極板 | 導電/耐蝕/輕量化 | Φ0.1-0.3mm編織網 | 接觸電阻<5mΩ·cm2,壽命>20,000h |
電解水制氫電極 | 高催化活性 | 多孔鈦絲(孔隙率60-80%) | 過電位@10mA/cm2<200mV |
液流電池集流體 | 耐強酸/低電阻 | Φ0.5mm梯度鍍層鈦絲 | 釩電解液腐蝕速率<0.01mm/年 |
鈣鈦礦光伏導線 | 柔性/耐濕熱 | Φ0.08mm超細鈦包銅絲 | 耐85℃/85%RH老化>1000h |
2. 材料性能對比(鈦絲 vs 傳統材料)
性能指標 | 鈦絲(Gr.1) | 不銹鋼316L | 石墨復合板 |
質量密度(g/cm3) | 4.51 | 8.0 | 1.8 |
導電率(%IACS) | 3.1 | 2.5 | 120(各向異性) |
腐蝕電流密度(μA/cm2) | 0.05(1M H?SO?) | 1.2 | 不適用 |
成本($/kg) | 45-60 | 8-12 | 25-40 |
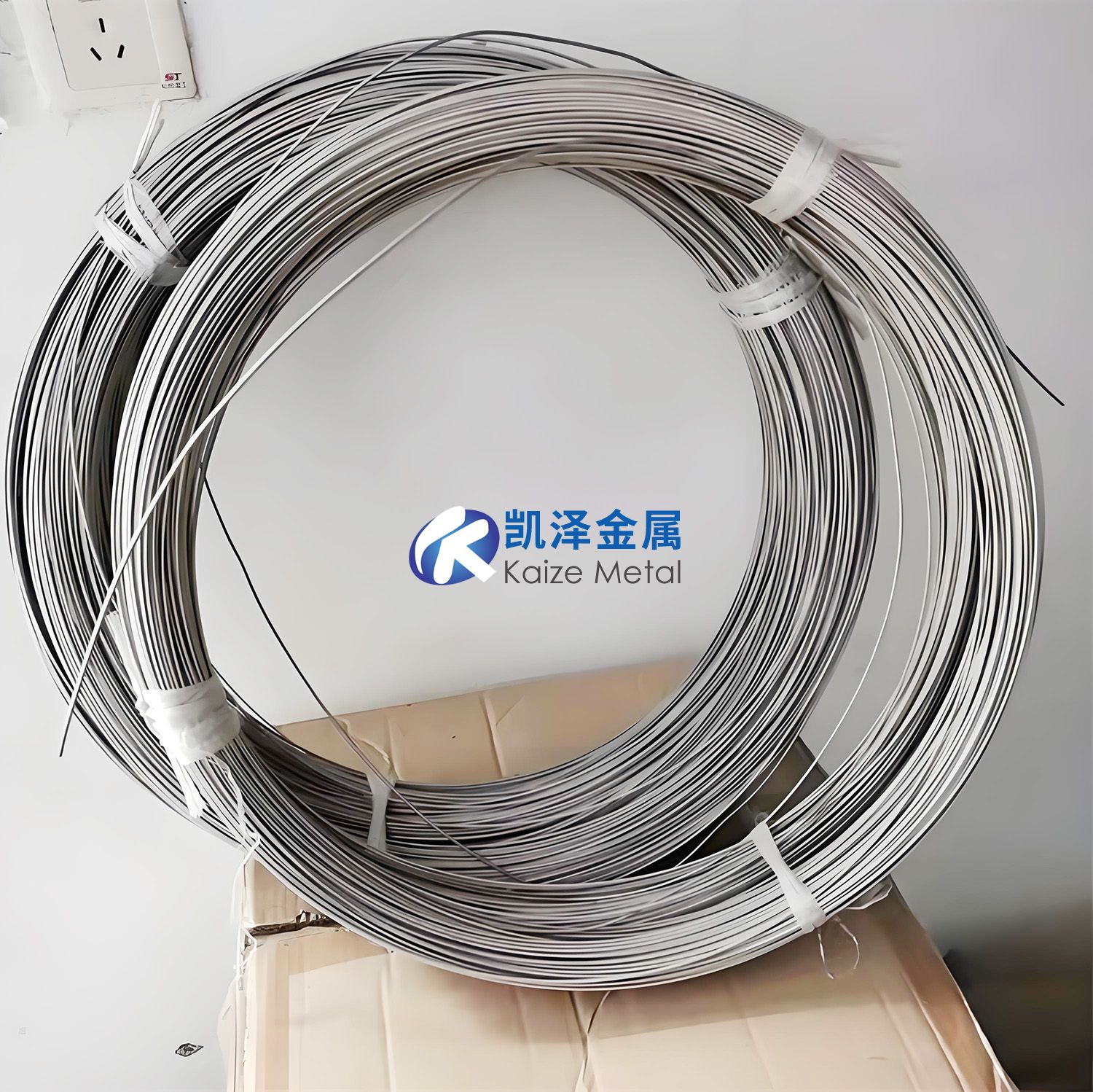
3. 關鍵制備技術突破
工藝環節 | 傳統方法 | 2023年創新技術 | 效益提升 |
絲材拉拔 | 多道次冷拔(減面率20%) | 等徑角軋制(ECAR)+深冷處理 | 抗拉強度↑30%(達800MPa) |
表面改性 | 酸蝕粗糙化 | 飛秒激光微納結構(孔徑<500nm) | 電化學活性面積↑5倍 |
復合加工 | 機械包覆 | 磁控濺射+電沉積(Pt/TiN梯度層) | 析氫效率提升至98% |
焊接技術 | TIG點焊 | 微束等離子弧焊(電流<10A) | 熱影響區<50μm |
4. 產業化應用案例
應用項目 | 技術方案 | 性能指標 | 經濟性分析 |
豐田Mirai雙極板 | Ti絲編織體(Φ0.15mm) | 功率密度4.4kW/L | 單輛車用量1.2kg,降本$320 |
成本降低40% vs 石墨 |
中石化PEM制氫 | 3D打印多孔鈦絲電極 | 制氫效率75% @2A/cm2 | 設備壽命延長至8年(ROI<3年) |
大連液流電池 | 鍍釕鈦絲集流體 | 能量效率>85% | 運維成本下降25%/MWh |
隆基Hi-MO 7組件 | 鈦包銅柵線(Φ0.08mm) | 組件效率23.6% | BOM成本增加$0.02/W,溢價$0.05/W |
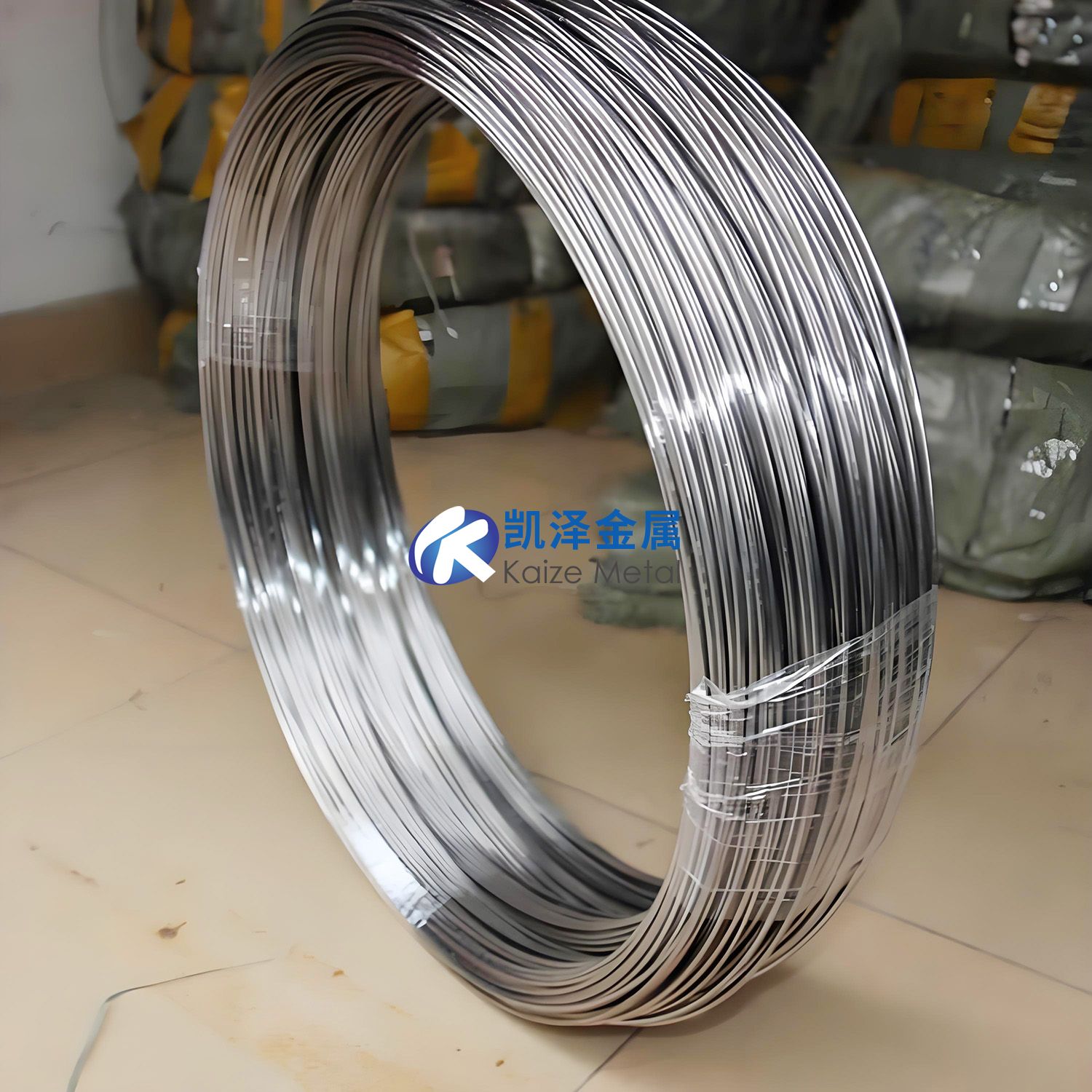
5. 技術挑戰與攻關方向
技術瓶頸 | 核心問題 | 前沿解決方案 |
成本控制 | 海綿鈦價格波動大 | 短流程制備(電子束冷床爐→直接拉絲) |
界面穩定性 | 鈦/催化劑層剝離 | 原子層沉積(ALD)界面強化 |
超細絲量產 | Φ<0.05mm斷絲率高 | 微流體動態成形技術(MIT最新成果) |
回收再利用 | 廢絲重熔污染 | 氫化脫氧(HDH)閉環工藝 |
6. 國內外產業布局對比
維度 | 中國(2023) | 國際先進水平 | 差距分析 |
超細絲產能 | Φ0.1mm級(200噸/年) | Φ0.05mm級(日本神戶制鋼) | 斷絲率高3倍 |
表面鍍層技術 | 微米級梯度鍍層 | 納米多層結構(德國賀利氏) | 壽命差40% |
裝備自主化 | 依賴進口拉絲機(80%) | 全流程自主(美國SMC) | 精度低1級 |
專利儲備 | 氫能領域56件 | 日本住友289件 | 核心專利率<20% |
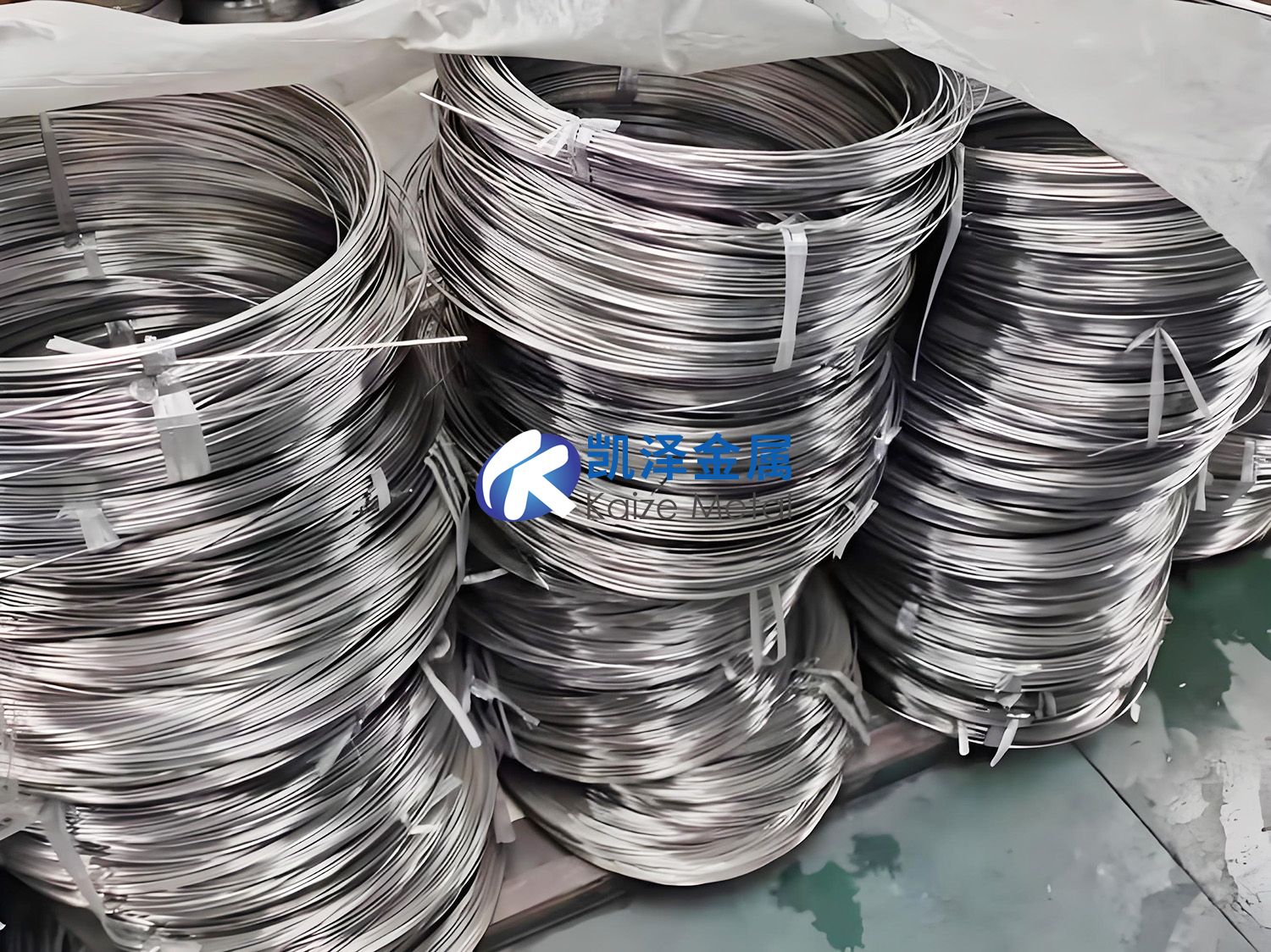
7. 未來技術路線圖
時間節點 | 技術方向 | 目標參數 | 應用場景 |
2025 | 非晶鈦絲 | 強度>1.5GPa | 微型燃料電池 |
電阻率↓30% |
2027 | 智能鈦絲 | 應變自感知(精度±0.1%) | 電池健康監測 |
2030 | 月壤鈦絲 | 原位還原制備(純度>99.9%) | 太空能源站 |
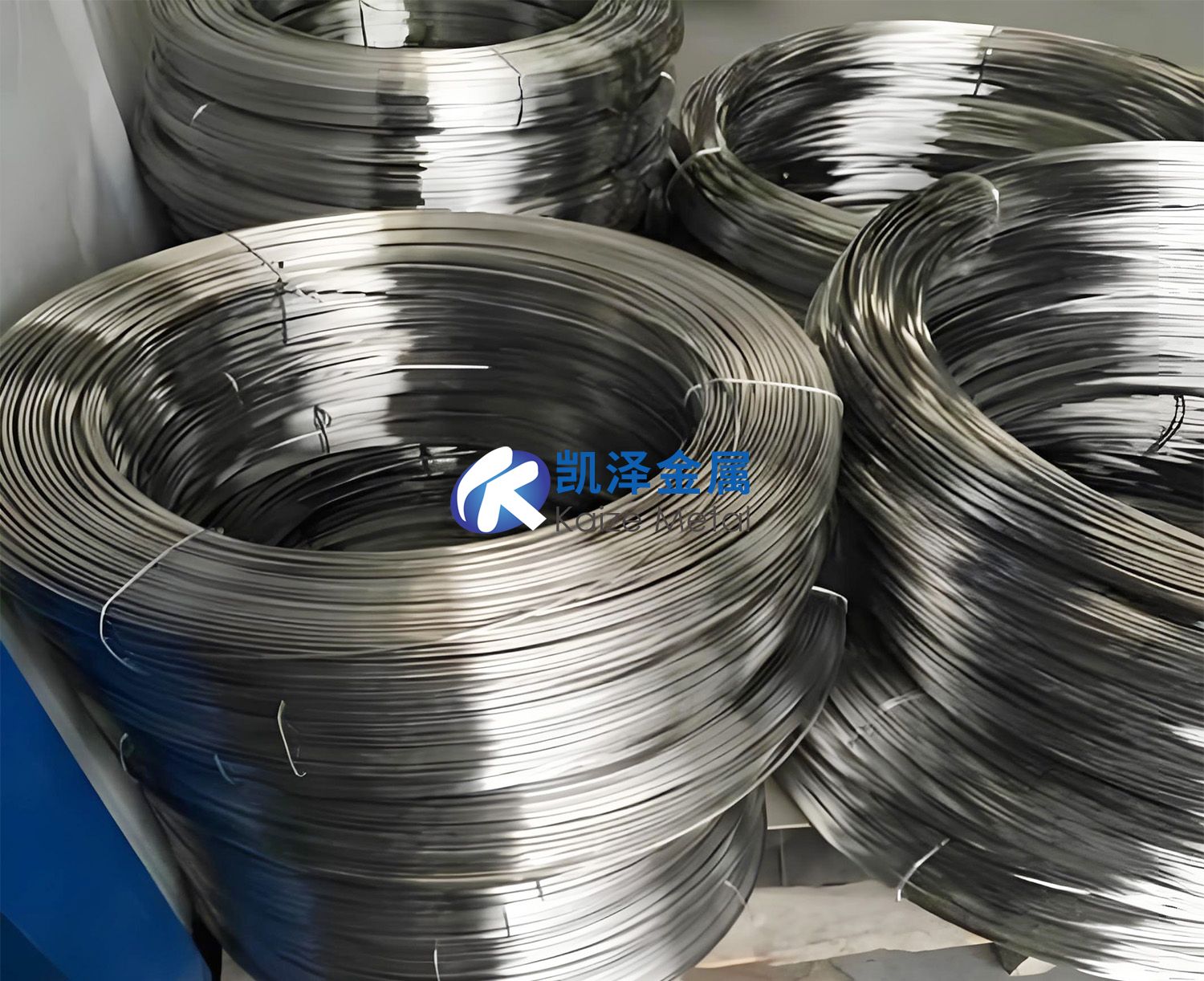
新能源用鈦絲通過材料改性與結構創新,在氫能、儲能領域展現出顛覆性潛力。建議優先突破超細絲精密制造與表面催化功能化技術,同時布局太空級鈦絲等前沿方向。需警惕石墨烯復合材料的替代風險,通過政產學研協同加速產業化進程。
相關鏈接