1、前言
鈦合金具有很高的強度質量比及耐蝕性,在航空產品中有廣泛的應用?鈦合金硬度低?耐磨性能差,對于有耐磨性能要求的軸類?桶類零件,需在鈦合金表面進行鍍鉻,以提高其表面硬度和耐磨性能?鈦是非常活潑的金屬,與空氣中的氧和氮易生成薄而致密的鈍化膜,這層鈍化膜會阻礙電鍍的進行?為避免鈍化膜對鈦合金電鍍鉻的影響,多采用轉化膜+預鍍層工藝對鈦合金進行前處理?
目前,在生產中應用較多的電鍍鉻前處理工藝為活化+氫化處理+鍍乳白鉻,但在實際零件生產中,受多種因素影響,鈦合金電鍍鉻零件產品合格率仍不穩定?且氫化處理工藝采用純硫酸與純鹽酸配制高純酸液,溶液去除量大,危險性高,使用時溫度控制范圍較窄,既容易影響到零件尺寸,又容易造成安全事故?為優化鈦合金電鍍前處理工藝,避免氫化處理工藝存在的缺陷,對理論上膜層穩定性更好的氟化處理工藝進行了研究?
2、試驗
2.1試驗配方
表1 轉化膜工藝配方
序號 | 成分濃度 | 溫度 (℃) | 時間 (min) | 備注 |
1 | H?SO? 250ml/L HCl 750ml/L | 18~25 | 60~90 | TC2氧化處理用 |
2 | H?SO? 650ml/L HCl 350ml/L | 18~25 | 60~90 | TC8氧化處理用 |
3 | Na?PO?+12H?O 40 g/L NaF 20 g/L CH?COOH 30 ml/L | 25~35 | 8~10 |
|
4 | RLD-1100 100ml/L | 室溫 | 2~4 |
|
5 | K?Cr?O? 250g/L HF 48ml/L | 82~100 | 20 | B481~68 |
鑒于除油?吹砂?預鍍層(鍍乳白鉻)?熱處理工藝為鈦合金電鍍通用處理工藝,且按照以往生產經驗,也未發生過只有鍍硬鉻層脫落,乳白鉻層未脫落現象,因此,鈦合金鍍鉻前處理工藝主要研究對象為活化工藝及轉化膜工藝?
現有零件均為經過了精密機械加工的零件,且經過吹砂,氧化膜較薄,因此可不采用活化工藝,而是在吹砂后直接進行轉化膜工藝?轉化膜工藝配方見表1,活化工藝配方見表2?
表2 活化工藝配方
序號 | 硝酸 | 鹽酸 | 氫氟酸 | 工藝條件 | 備注 |
1 | - | 50ml/L | 30ml/L | 室溫 30~45s | TC2氧化處理用 |
2 | 500ml/L | - | 50ml/L | 室溫 1~2min | ASTM B481~68 |
2.2選型試驗方案
鈦合金鍍鉻工藝主要應用于有一定耐磨要求的鈦合金表面的防護,從設計指標上主要要求其具有較高的結合強度?對基體的疲勞影響較小,從工藝上其處理工藝主要要求其對基體的去除量較小?因此采用TC2?TC6?TC18圓柱試料?棒狀試料進行試驗,分別考察每組試驗中試料的基體去除量?電鍍后鍍層結合力(熱震法)?
基體去除量:在處理前?后對試樣進行稱重,計算基體表面去除量?
熱震法測結合力:將試樣加熱到300℃,保溫0.5h,放入室溫水中驟冷?
試樣圖片見圖1?圖2?
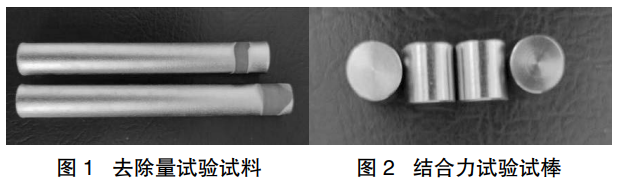
2.3 性能對比試驗方案
采用脈沖加熱熱導氫測定儀測定試樣氫含量,試樣鍍鉻層厚度 80 ~ 100μm,試樣尺寸為 4mm×4mm×2mm。按照 HB5143《金屬室溫拉伸試驗方法》對電鍍鉻后的試樣進行拉伸,試樣光桿區域鍍鉻層厚度 80 ~100μm,試樣如圖 3 所示。
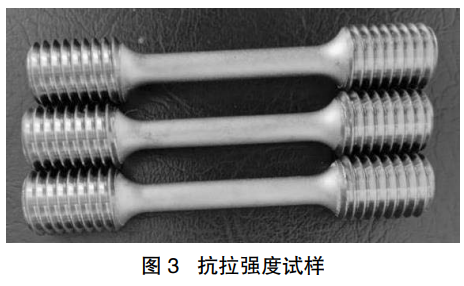
3、結果與討論
3.1選型試驗結果
在選型試驗中,采用ASTMB481-68高濃度的硝酸氫氟酸活化工藝(活化工藝3)?重鉻酸鉀-氫氟酸轉化膜工藝時(轉化膜工藝5),反應劇烈,產生大量氣泡-氮氧化物紅煙,去除量較大(活化工藝單面去除量>2μm,轉化膜工藝單面去除量>4μm)?且考慮到氫氟酸有較大安全風險,硝酸?重鉻酸鉀屬于易制爆化學品,采購及存儲存在一定困難,未進行后續試驗?
表3 TC2材料選型試驗結果
活化工藝 | 轉化膜工藝 | 去除量 (單面/μm) | 結合力 |
| 磷酸鈉-氟化鈉-醋酸 | 鹽酸-氫氟酸活化:<1.2 硝酸-氫氟酸活化:<1.2 磷酸鈉-氟化鈉-醋酸:<0.6 RLD-1100:<3.8 | 吹砂后乳白鉻層脫落 |
鹽酸氫氟酸 | RLD-1100 | 熱震試驗通過 |
硝酸氫氟酸 | 磷酸鈉-氟化鈉-醋酸 | 吹砂后乳白鉻層脫落 |
RLD-1100 | 熱震試驗通過 |
不活化 | 磷酸鈉-氟化鈉-醋酸 | 吹砂后乳白鉻層脫落 |
RLD-1100 | 熱震試驗未通過 |
表4 TC6材料選型試驗結果
活化工藝 | 轉化膜工藝 | 去除量(單面/μm) | 結合力 |
硝酸氫氟酸 | 磷酸鈉-氟化鈉-醋酸 | 硝酸-氫氟酸活化:<1.2 磷酸鈉-氟化鈉-醋酸:<0.6 RLD-1100:<3.8 | 吹砂后乳白鉻層脫落 |
RLD-1100 | 熱震試驗通過 |
不活化 | 磷酸鈉-氟化鈉-醋酸 | 吹砂后乳白鉻層脫落 |
RLD-1100 | 熱震試驗通過 |
試驗結果表明對于TC2材料,不采用活化工藝時,采用各種轉化膜工藝均不能獲得結合力良好的鍍層;采用磷酸鈉-氟化鈉-醋酸配方時,均不能獲得結合力良好的乳白鉻層;采用鹽酸-氫氟酸活化或硝酸-氫氟酸活化?RLD-1100轉化膜時,均可獲得結合力良好的鍍層?但考慮到硝酸-氫氟酸活化溶液濃度較高,且需使用易制爆品硝酸,最終選擇鹽酸-氫氟酸活化+RLD-1100轉化膜作為優選工藝?
對于TC6?TC18材料,不采用活化工藝時,采用RLD-1100轉化膜時,也可獲得結合力良好的鍍層?采用磷酸鈉-氟化鈉-醋酸轉化膜時,均不能獲得結合力良好的鍍鉻層,不采用硝酸-氫氟酸活化工序,可避免使用易制爆品硝酸及危險性較大的氫氟酸,去除量及吸氫量也更小,最終選擇RLD-1100轉化膜作為優選工藝?
3.2氫化處理與氟化處理性能對比試驗結果
氫含量?結合強度?抗拉強度試驗(含斷面收縮率?斷后伸長率)結果分別見表6?表7?表8?
表5 TC18材料選型試驗結果
活化工藝 | 轉化膜工藝 | 去除量(單面/μm) | 結合力 |
硝酸氫氟酸 | 磷酸鈉-氟化鈉-醋酸 | 硝酸-氫氟酸活化:<2.8 磷酸鈉-氟化鈉-醋酸:<0.6 RLD-1100:<2.8 | 吹砂后乳白鉻層脫落 |
| RLD-1100 | 熱震試驗通過 |
不活化 | 磷酸鈉-氟化鈉-醋酸 | 吹砂后乳白鉻層脫落 |
| RLD-1100 | 熱震試驗通過 |
表6 基體氫含量
基體材料 | 氫含量(<0.015%) | 氫化處理工藝(%) | 氟化處理工藝(%) |
TC2 | 0.011 | 0.011 | 0.011 |
TC6 | 0.011 | 0.011 | 0.012 |
TC18 | 0.012 | 0.012 | 0.012 |
表7 鍍層結合強度
基體材料 | 結合強度(Mpa) | 氫化處理工藝工藝 | 氟化處理工藝 |
TC2 | 61.34 | 61.51 |
|
TC6 | 63.11 | 63.66 |
|
TC18 | 62.72 | 65.91 |
|
表8:抗拉強度試驗結果
材料 | 抗拉強度 (Mpa) | 抗拉強度 (Mpa) | 斷面收縮率 (%) | 斷后伸長率 (%) | 抗拉強度 (Mpa) | 斷面收縮率 (%) | 斷后伸長率 (%) |
TC2 | 811.13 | 769 | 41.8 | 17.8 | 765 | 41.4 | 19 |
TC6 | 1221.02 | 1096 | 44.8 | 18.6 | 1089 | 46.2 | 17 |
TC18 | 1213.95 | 1020 | 45 | 19.89 | 1036 | 47.2 | 19.4 |
由表6可知,TC2?TC6?TC18鈦合金電鍍鉻后,基體氫含量數值均未超過0.015%的要求值,但數值均相對較高?理論上氟化處理時間更短,酸液濃度更低,基體含氫量應更低,但電鍍鉻時間長?電流效率低,是基體吸氫的主要來源,且電鍍鉻層厚度可能有一定波動,因此決定基體氫含量的更多是鍍鉻工序,可認為經2種前處理工藝后基體含氫量基本相當?
由表7可知,TC2?TC6?TC18鈦合金鍍鉻層的結合強度均在60~66MPa范圍內,采原氟化處理工藝電鍍的鍍層結合強度與采用氫化工藝電鍍的鍍層結合強度基本相當,沒有明顯差距?
由表8可知,對于TC2?TC6?TC18鈦合金,不論采用何種前處理工藝,基體的抗拉強度均會有所下降?經2種前處理工藝處理后,TC2材料基體抗拉強度基本一致?經2種前處理工藝處理后,經氫化處理的TC6鈦合金基體的抗拉強度稍高于經氟化處理工藝處理的基體,經氫化處理的TC18鈦合金基體的抗拉強度稍低于經氟化處理工藝處理的基體?對于TC2?TC6?TC18鈦合金,不論采用何種前處理工藝,伸長率和斷面收縮率均會有所下降?經2種前處理工藝處理后,3種材料的伸長率和斷面收縮率均相差很小,且滿足伸長率≥10%,斷面伸縮率≥23%的要求?考慮到試棒尺寸存在一定偏差?鍍層厚度也存在一定偏差,可能導致的基體抗拉強度變化,可認為經2種前處理工藝后電鍍鉻的基體抗拉強度基本相當,伸長率?斷面收縮率基本相當,沒有明顯差距?
4、結語
對于TC2材料,采用鹽酸-氫氟酸活化+RLD-1100氟化處理液,可獲得結合強度良好的鈦合金鍍鉻鍍層?對于TC6?TC18材料直接采用RLD-1100氟化處理液,即可獲得結合強度良好的鈦合金鍍鉻鍍層?采用RLD-1100氟化處理并電鍍的基體,其基體含氫量?抗拉強度與采用氟化處理并電鍍的基體性能相當?
參考文獻:
[1]孫志華,劉佑厚,張曉云等。鈦及鈦合金的電鍍工藝述評[J].腐蝕與防護,2005,26(11):493-496.
[2]湯智慧,王長亮,貢興嘉等。電鍍硬鉻工藝對TC6鈦合金性能的影響研究[J].航空材料學報,2012,32(4):49-52.
[3]李博。提高鈦合金零件鍍鉻層結合力的方法[J].電鍍與精飾,2014,36(3):26-28.
[4]楊鵬,趙金航,王娟。提高鈦合金零件鍍鉻結合力[J].電鍍與精飾,2015,37(8):28-31.
[5]郭初陽,郭喜軍,王永紅等。鈦合金零件鍍鉻工藝及控制研究[J].新技術新工藝,2015,10:96-99.
相關鏈接