1、序言
大型鍛件的調質處理往往比小鍛件的熱處理更加困難,某大型環形薄壁鍛件尾環殼體(以下簡稱 “工件”)是固體火箭發動機上的核心零件。在發動機運行過程中,工件一方面要支撐擴張段絕熱層,增加其強度;另一方面,對于柔性噴管,其擺動時殼體大端還要承受伺服作動器作用的集中力。同時,其剛度還要滿足伺服作動器的控制精度。該工件直徑較大,厚度較薄,調質過程中易變形,且變形后無法進行校正。另外,其硬度要求較高,且不允許多次淬火。本文從熱處理工藝、工裝設計和生產過程三個方面進行探討,從工藝和工裝適用性方面,來提高工件的整體質量。
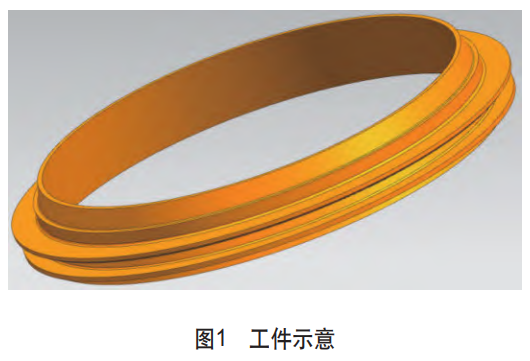
2、工件介紹
工件材質為 30CrMnSiA 鋼,最大直徑為 1630mm,高為 230mm,壁厚約 25mm。
技術要求:硬度 33~38HRC。
變形要求:翹曲變形不得超過 3.28mm。
表面質量:不允許存在麻點、裂紋等缺陷。
30CrMnSiA 鋼的化學成分見表 1。
表 1 30CrMnSiA 鋼的化學成分(質量分數 %)
C | Cr | Mn | Si | P | S |
0.28~0.34 | 0.80~1.10 | 0.80~1.10 | 0.90~1.20 | ≤0.02 | ≤0.02 |
3、工藝制定
大型鍛件的調質多數情況下是作為最終熱處理,賦予大型鍛件的最終性能。因此,對其進行熱處理必須嚴謹,大鍛件的內部存在較多缺陷,鍛件的尺寸和重量越大,合金成分越多,缺陷問題就越嚴重。本文所討論的就是關于 30CrMnSiA 鋼的大型環形鍛件的調質處理。
3.1 淬火工藝
(1)淬火溫度:與小鍛件相比,大型鍛件熱處理過程中更容易出現問題,其內部存在較多的冶金缺陷,對于整只鋼錠鍛造成的鍛件,加熱時往往采用規定溫度的上限 [1]。
(2)加熱方式:在大型鍛件進行熱處理時,對其有效截面尺寸進行計算分析,控制好裝爐溫度和加熱速度。通常對于有效截面尺寸小的鍛件,裝爐時不限制升溫速度。對于合金元素含量高的鍛件,必須選擇階梯加熱的方式。按照常規熱處理經驗,選定 650℃為中間均溫溫度。
(3)均溫與保溫:當儀表到達工藝溫度時,就意味著均溫開始。一般均溫時間選擇 1~1.5 倍保溫時間。保溫時間的選取則按照工件的有效截面尺寸來確定,保溫時間一般按 0.8~1.0h/100mm 選取。中高合金鋼取上限,低合金鋼取下限。該工件淬火工藝的淬火溫度階段的保溫時間為 1~1.5h。
(4)淬火冷卻:大型鍛件淬火時,首先最關鍵在于冷卻速度,其次是終冷溫度 [2]。對于合金鋼鍛件,一般選擇油淬,鍛件在油中冷卻速度比在水中小,因此工件內外溫差小,可顯著減小工件開裂和變形的傾向。淬火冷卻時間很大程度上決定了工件的熱處理效果,若時間過短,則工件性能達不到所需要求;若時間過長,終冷溫度過低,則會加大工件淬裂的危險性 [3]。終冷溫度與工件的內在質量有關,為此選取 50~80℃為終冷溫度。
基于以上分析,該工件最終淬火工藝相關參數為 900±10℃油淬,經歷升溫均溫、升溫、保溫階段,保溫時間 1~1.5h。
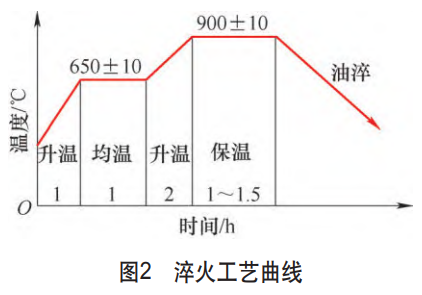
3.2 回火工藝
大型鍛件淬火后應及時回火,防止工件開裂,原則是不超過 2h。淬火后回火是為了獲得最終力學性能,并消除內應力,獲得穩定的回火組織 [4],以達到工件的技術要求。
(1)回火溫度選擇:大型鍛件的回火溫度依照組織、性能的要求確定,可以進行工藝試驗再確定回火溫度。
(2)回火均溫、保溫時間:大型鍛件回火時,應依據工件形狀的復雜程度來控制升溫速度,有時為了防止工件中缺陷擴大,在 350℃保持一定的時間,然后再升高到工件回火溫度 [5]。工件回火保溫時間一般是與工件有效截面有關,在 300~600℃回火時,空氣爐中的保溫時間為 40~60min 加上最大厚度乘以 2~3min/mm。該工件回火工藝的總保溫時間為均溫時間加上保溫時間,共 4~6h。
(3)回火冷卻:對于 30CrMnSiA 鋼,回火冷卻選用水冷或油冷均可。通常冷卻速度為:水冷 > 油冷 > 空冷 > 爐冷,隨著冷卻速度的增大,洛氏硬度逐漸增大,沖擊韌度逐漸提高。為獲得較高硬度,回火采用水冷方式。
該工件最終回火工藝相關參數為 500~520℃水冷,經歷升溫、保溫階段,保溫時間 4~6h。
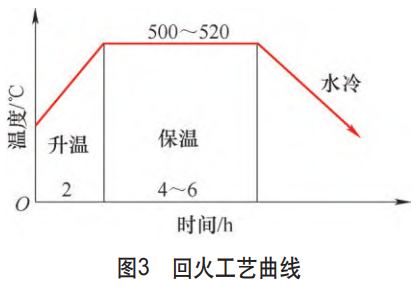
3.3 爐型的選擇
根據工藝要求及工件尺寸大小,選擇型號為 RT3-265-10 的全纖維臺車爐,該設備為 Ⅲ 類爐,額定溫度為 1000℃,額定功率為 265kW,有效尺寸為 2200mm×1800mm×900mm,能夠滿足工藝的溫度范圍要求及工件的尺寸要求。
4、工裝設計
4.1 外形設計
由于工件呈環形,在高溫起吊過程中,受到不均勻的力會導致工件嚴重變形,因此在設計工裝時,就設計成一個頂端起吊結構形式。
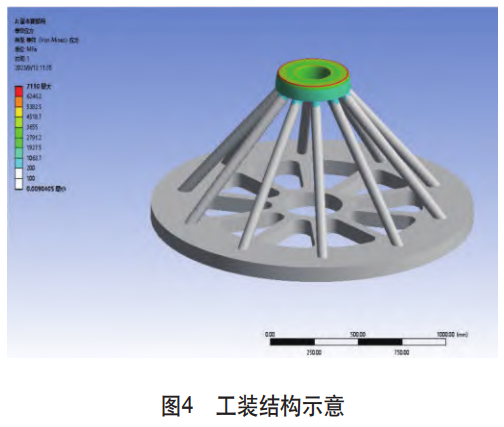
工裝由上圓板、下圓板和鋼管焊接而成,頂端的圓板用于起吊。該外形工裝能夠對工件起全支撐作用,以保證工件在高溫起吊過程中均勻受力,從而降低工件的變形量。另外,在起吊工件時,鋼管焊接部分能夠對工件起到固定作用,保證工裝使用的安全性。
4.2 強度計算
設計的工裝要進行強度計算,避免在高溫起吊過程中,工裝因受力過大失效,而造成人員傷亡。
對工裝進行有限元分析,邊界條件設置為工裝上表面起固定支撐,按照所承受工件重力,對工裝下圓板上表面施加 2600N 的力,環境溫度按照工件淬火溫度設置,為 900℃。
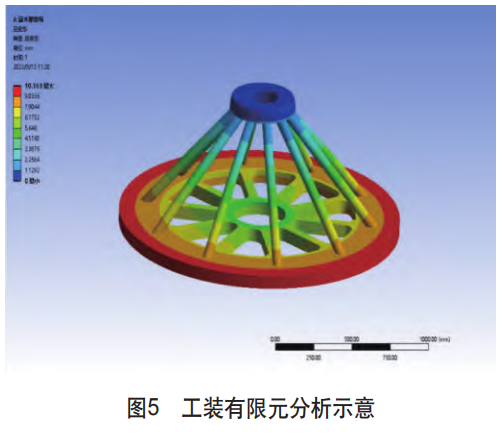
經過有限元分析計算,工裝上圓板受力較小,工裝下圓板受力較大,若在下圓板受力最大位置放置工件,則其變形量會達到 10.16mm,但工裝是均勻變形,高溫起吊過程中仍然能夠對工件起到均勻支撐的作用,因此工件的外形設計合格。要使工裝變形量減小,只需更換材料,將普通碳素鋼更換成耐高溫材料,或增大下圓盤厚度,這些都能改善工裝在起吊過程中的變形問題,并延長工裝的使用壽命。
在后續的使用過程中,逐漸對工裝進行改進,在工裝下圓盤上表面焊接相同尺寸的鐵棒,在淬火時,讓工件的底面能夠接觸到淬火冷卻介質,并添加不同尺寸的楔鐵作為調整工具,以延長工裝的使用壽命。
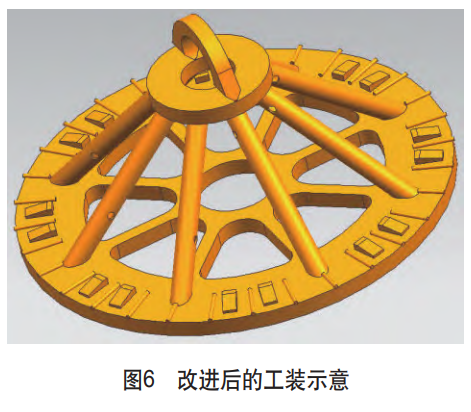
5、工件熱處理
5.1 生產操作
首先進行來件檢測,檢查工件表面是否有裂紋等明顯缺陷,檢查是否存在尖角。
將工件放置在專用工裝上,注意工件需平穩放置,工件底面需全接觸工裝,無接觸部分采用楔鐵墊平。工件和工裝一起進爐加熱,工裝在爐內也需放置平穩。起吊時需平穩升起,快速進入油槽淬火,注意冷卻時間,終冷溫度控制在 50~80℃,淬火后需進行硬度檢測,為回火溫度的選擇提供數據,淬火完成后應及時回火。
5.2 檢測結果
采用此工藝和工裝,調質完成 6 件工件,依次對其進行硬度和翹曲變形檢測,并對同爐試樣采用光學顯微鏡進行金相分析。硬度檢測淬火硬度和回火硬度,檢測設備使用便攜式硬度計,檢測點位為圓周方向 90°,間隔檢測小端 A 面和大端 B 面共 4 點;變形檢測工件小端 A 面、大端 B 面及內錐面 C 面,每面檢測 8 個點位,沿圓周方向均勻分布。
30CrMnSiA 鋼經 900℃淬火和 500~520℃回火后的金相組織均勻。
硬度和翹曲變形檢測數據統計分別見表 2 和表 3。
表 2 硬度檢測數據統計(HRC)
工件編號 | 檢測點 | 檢測點 |
| A1 | B1 | A2 | B2 | A1 | B1 | A2 | B2 |
1# | 45.2 | 43.6 | 45.8 | 44.1 | 36.8 | 35.7 | 37.6 | 36.1 |
2# | 45.5 | 44.3 | 45.7 | 44.2 | 37.2 | 36.5 | 37.1 | 36.3 |
3# | 46.2 | 45.4 | 45.6 | 45.3 | 38.0 | 37.3 | 37.4 | 37.2 |
4# | 44.8 | 45.6 | 45.8 | 43.6 | 36.8 | 37.5 | 37.8 | 35.4 |
5# | 45.2 | 44.6 | 44.1 | 44.3 | 37.1 | 36.7 | 36.3 | 36.4 |
6# | 45.5 | 43.9 | 45.6 | 45.6 | 37.3 | 35.7 | 37.5 | 37.1 |
表 3 翹曲變形檢測數據統計(mm)
工件編號 | 檢測面 | 檢測點 |
|
| 1 | 2 | 3 | 4 | 5 | 6 | 7 | 8 |
1# | A | 1.2 | 1.7 | 1 | 0.3 | 1.3 | 2 | 0.8 | 0.6 |
B | 0.2 | 1 | 1 | 1.7 | 1.6 | 0 | 2 | 2.7 |
C | 1.5 | 1 | 1.2 | 1.1 | -0.3 | 0 | 1 | 1.2 |
2# | A | 1.1 | 1.6 | 1.2 | 0.3 | 1.2 | 1.1 | 0.5 | 1.1 |
B | 1.2 | 1.8 | 1.2 | 0.3 | 1.8 | 1.8 | 0.4 | 0.1 |
C | 1.4 | 1.9 | 1.3 | -0.1 | 1.7 | 1.5 | -0.2 | 0 |
3# | A | 1.3 | 1.5 | 0.3 | 1.3 | 1.5 | 0.4 | 0.1 | 1.6 |
B | 1.3 | 1.8 | 1.5 | 2 | 3 | 0.4 | 1.6 | 0.1 |
C | 1.4 | 1 | 1.3 | 1.5 | 0.7 | -1.4 | 0.2 | 0.5 |
4# | A | 0.2 | 1.3 | 1.8 | 1.9 | 1 | 1.6 | 0.7 | 2 |
B | 1.9 | 2.1 | 0.3 | 0.8 | 1.5 | 0.7 | 2.3 | 1.6 |
C | 0.3 | 0.8 | -0.1 | 0.3 | 0.8 | 1.1 | 1.3 | 1.1 |
5# | A | 1.5 | 1.8 | 0.9 | 1.2 | 2 | 1.6 | 0.7 | 1.4 |
B | 0.8 | 1.2 | 2.2 | 1.6 | 1.7 | 0.4 | 1.8 | 1.5 |
C | 1.1 | 1.6 | 1.5 | 0.4 | 0.7 | 1.3 | 0.6 | 0.5 |
6# | A | 2.1 | 1.5 | 1.8 | 1.3 | 2.2 | 0.8 | 1.3 | 1 |
B | 1.5 | 0.6 | 1.3 | 1.1 | 1.6 | 1.3 | 0.9 | 0.4 |
C | 1.5 | 1.2 | 0.8 | 0.9 | -0.2 | 1.4 | 1.5 | 0.5 |
由表 2 可知,A 面淬火和回火后硬度普遍高于 B 面,且回火后所有工件硬度均控制在 35~38HRC,滿足工件 33~38HRC 的要求。
由表 3 可知,3# 工件 B 面的第 5 點變形量最大,達到 3mm,在要求的 3.28mm 范圍內。
從金相組織可看出,經 900℃淬火和 500~520℃回火后的金相檢測組織為均勻的回火索氏體。
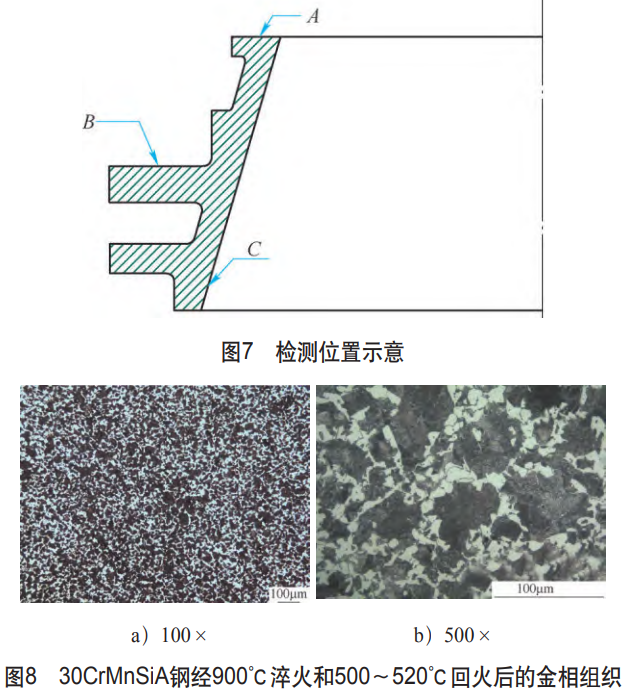
6、結束語
1)大型環形鍛件在熱處理過程中極容易變形,且有效壁厚越薄,變形量越大。淬火時采用階梯式升溫的方法可有效減小熱應力。
2)裝爐方式對工件的變形量有較大影響,因此裝爐時應注意工件或工裝是否能夠全面接觸熱處理爐支撐平臺,保證加熱時受力均勻。
3)工件在淬火起吊時需平穩,保證起吊過程受力均勻,淬火時控制好油淬時間,掌握終冷溫度,淬火后還需檢測淬火硬度,且淬火后盡快開始回火。
參考文獻
[1] 耿學明,黎定旺。大型鍛件的調質熱處理實踐 [J]. 金屬加工 (熱加工),2010 (5):40 - 41,45.
[2] 李曉宏,楊迪,黃守己。大型環類鍛件調質處理 [J]. 大型鑄鍛件,2018 (2):26 - 27,35.
[3] 沈黃富。關于大型鍛件調質熱工藝的探討 [J]. 金屬熱處理,1982 (8):27 - 33.
[4] 齊加勝。淬回火對 30CrMnSiA 高強鋼組織與力學性能的影響 [J]. 熱加工工藝,2022,51 (24):125 - 128.
[5] 吳子愷,陳偉,周海銘,等。回火溫度對 30CrMnSiA 鋼力學性能的影響 [J]. 金屬熱處理,2019,44 (4):163 - 167.
相關鏈接