綜合鈦棒材料特性、制造工藝與應(yīng)用前沿,凱澤金屬將航空結(jié)構(gòu)件(軸類、銷釘、齒輪)用鈦棒材料的系統(tǒng)性技術(shù)分析如下:
一、核心材質(zhì)概述
航空軸類、銷釘及齒輪用鈦棒以TC4(Ti-6Al-4V)為主導(dǎo),占比超80%,輔以TA7(Ti-5Al-2.5Sn) 及TC11(Ti-6.5Al-3.5Mo-1.5Zr-0.3Si) 等高強耐熱合金。其核心優(yōu)勢在于:
比強度卓越:TC4抗拉強度≥895MPa,密度僅4.44g/cm3,替代結(jié)構(gòu)鋼可減重30%;
耐蝕性突出:表面致密氧化膜抵御海洋大氣腐蝕,年腐蝕率<0.001mm/a,鹽霧壽命超2400小時;
高溫穩(wěn)定性:TA7在500℃仍保持屈服強度>550MPa,適用于發(fā)動機高溫區(qū)齒輪。
當(dāng)前技術(shù)瓶頸集中于耐磨性不足(摩擦系數(shù)0.4-0.6)與加工硬化(磨削比僅1.53,為鋼的1/50)。未來趨勢聚焦增材制造與涂層復(fù)合化,推動服役壽命提升及成本優(yōu)化。
二、名義成分與核心性能
(1)化學(xué)成分與國際牌號
牌號 | 國內(nèi)名義成分 | 國際對應(yīng) | 關(guān)鍵元素作用 |
TC4 | Ti-6Al-4V | ASTM Gr5 | Al穩(wěn)定α相提強度,V增強β相淬透性 |
TA7 | Ti-5Al-2.5Sn | AMS 4910 | Sn抑制高溫晶粒長大,提升蠕變抗力 |
TC11 | Ti-6.5Al-3.5Mo-1.5Zr-0.3Si | BT9 | Mo/Zr強化β相,Si細化晶粒提升耐熱性 |
雜質(zhì)控制:O≤0.20%,F(xiàn)e≤0.30%(航空級要求O≤0.12%)。
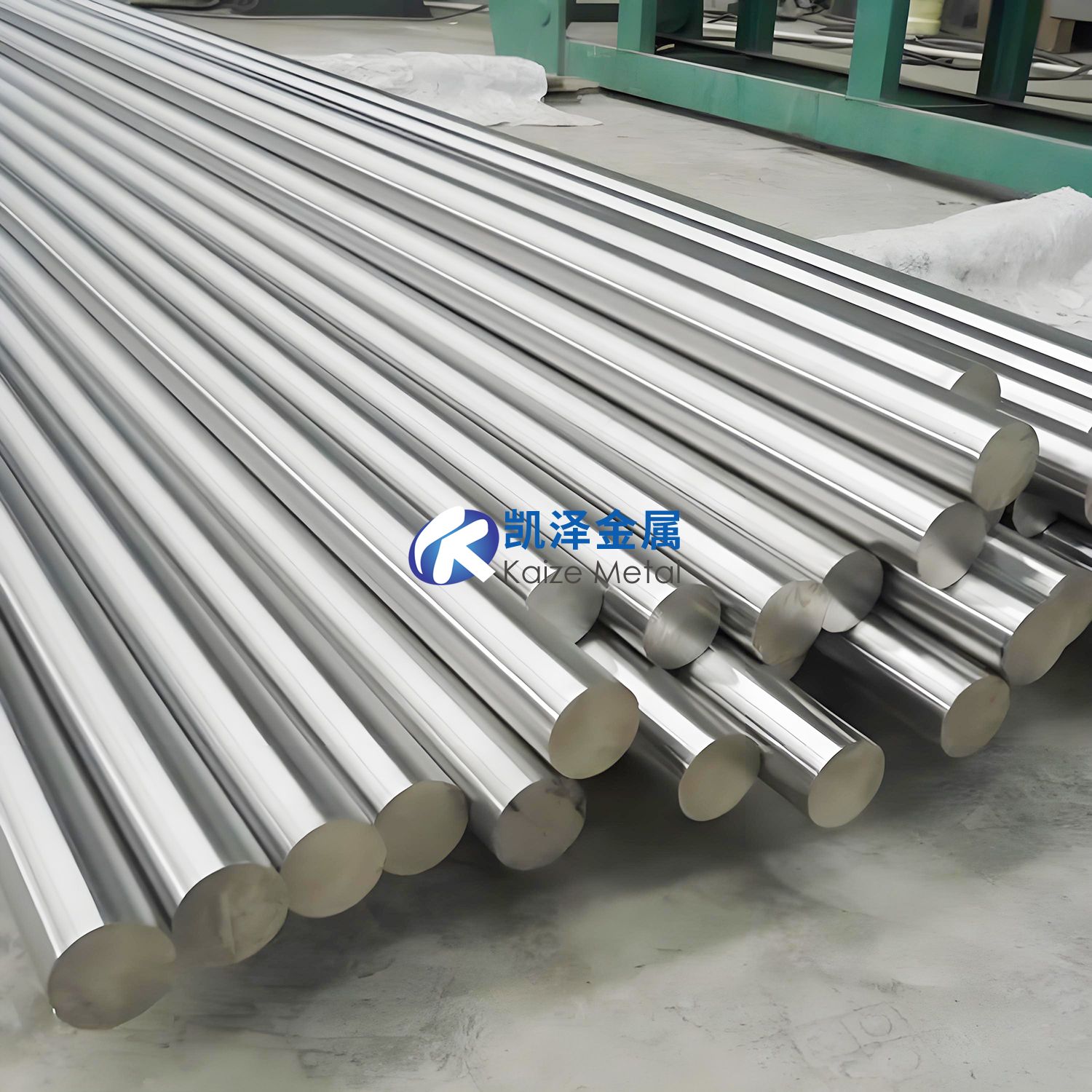
(2)物理與機械性能對比
性能 | TC4 | TA7 | TC11 |
密度 (g/cm3) | 4.44 | 4.46 | 4.48 |
熱導(dǎo)率 (W/m·K) | 7.8 | 8.1 | 6.9 |
抗拉強度 (MPa) | 895-1030 | 785-980 | 1030-1250 |
延伸率 (%) | ≥10 | ≥15 | ≥9 |
斷裂韌性 (MPa·m1/2) | ≥70 | ≥55 | ≥50 |
高溫強度 (500℃, MPa) | 520 | 550 | 780 |
(3)耐腐蝕性能
海洋環(huán)境:TC4在3.5% NaCl溶液中點蝕電位>1.2V(SCE),中性鹽霧試驗2400小時無點蝕;
應(yīng)力腐蝕:TA7的KISCC≥55MPa·m1/2(濕熱海洋環(huán)境臨界值);
高溫氧化:TC11在600℃氧化增重<2mg/cm2,形成Al?O?-TiO?復(fù)合保護膜。
三、加工注意事項
(1)切削與磨削關(guān)鍵技術(shù)
刀具選擇:
粗加工:硬質(zhì)合金涂層刀具(AlCrN基),前角8°-15°,切削速度30-50m/min;
精加工:Si?N?陶瓷刀具,線速度≥100m/min,配合70Bar高壓冷卻液。
磨削難點對策:
砂輪優(yōu)化:綠碳化硅或鈰碳化硅砂輪(粒度46#),水基乳化液流量>35L/min;
余量控制:精車留余量0.1mm,分粗磨(0.02mm/遍)、精磨(0.005mm/遍)。
(2)熱處理與表面強化
去應(yīng)力退火:真空爐750℃×2h,消除焊接殘余應(yīng)力>80%;
噴丸強化:鋼丸直徑2-5mm,產(chǎn)生785MPa表面壓應(yīng)力,疲勞強度提升30%;
耐磨涂層:WC-10Co-4Cr超音速噴涂(80-400μm)+ CrN磁控濺射(5-10μm),硬度>1800HV。
四、產(chǎn)品規(guī)格與制造工藝
(1)工業(yè)規(guī)格范圍
類型 | 直徑范圍 | 長度極限 | 執(zhí)行標(biāo)準(zhǔn) |
熱軋鈦棒 | φ50-500mm | 6000mm | GJB 2218A-2008 |
冷精軋鈦棒 | φ6-100mm | 3000mm | ASTM B348 |
增材制造 | 定制異形結(jié)構(gòu) | 16m2構(gòu)件 | AMS 4992D6 |
(2)核心工藝流程
傳統(tǒng)鍛造流程:
真空自耗熔煉(3次VAR)→ β相區(qū)鍛造(1050℃)→ 多向軋制 → 雙重退火(950℃+550℃)
控性要點:β鍛晶粒尺寸≤100μm,保證厚向強度差<50MPa。
增材制造革新:
大型構(gòu)件:北航16m2鈦框采用激光熔覆(功率10kW),成型效率提升80%,材料利用率85%;
冷熔合技術(shù):華曙高科ColdMetalFusion實現(xiàn)Ti64無支撐打印,孔隙率<0.5%。
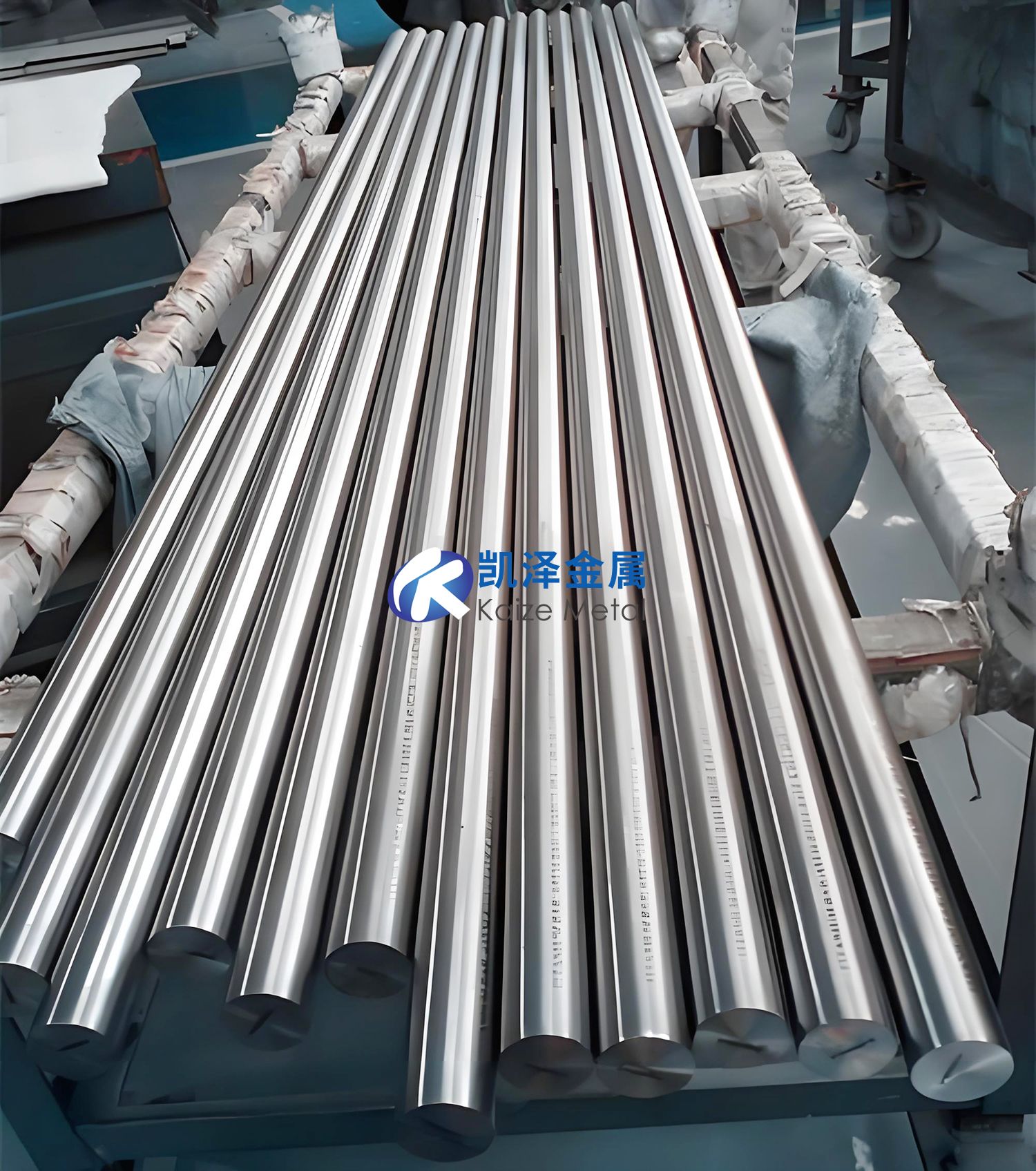
五、核心應(yīng)用與突破案例
(1)軸類件:抗微動腐蝕設(shè)計
案例:某型艦載機減速板作動筒軸,TC4基體+WC-10Co-4Cr/CrN復(fù)合涂層:
耐磨性:100N載荷磨損2h,質(zhì)量損失僅0.013g(無涂層TC4損失0.25g);
壽命:海洋環(huán)境服役周期從500小時延至5000小時。
(2)齒輪:高溫疲勞性能突破
案例:長江CJ-1000A發(fā)動機傳動齒輪(TC11材質(zhì)):
工藝:等溫鍛+滲氧處理(600℃×4h),表面硬度HRC55;
性能:600℃下疲勞強度達450MPa(提升40%)。
(3)銷釘:增材制造集成
案例:SpaceX星艦鈦合金定位銷:
工藝:SLM成型(層厚30μm),晶粒取向調(diào)控;
優(yōu)勢:比傳統(tǒng)銷釘減重45%,抗剪切強度≥670MPa。
六、先進制造工藝進展
超細晶鈦棒制備
多向鍛造:寶鈦集團開發(fā)8向模鍛技術(shù),晶粒細化至2-5μm,TC4延伸率提升至18%;
異步軋制:直徑φ100mm棒材心表晶粒度差≤0.5級,各向異性<3%。
復(fù)合涂層技術(shù)
梯度涂層:中科院開發(fā)TiB?/TiAlN多層濺射,摩擦系數(shù)降至0.15,適用高速齒輪;
原位氧化:TC4齒輪滲氧+激光重熔,表面硬度HV1200,耐溫提升至800℃。
綠色短流程工藝
氫化脫氫(HDH):殘鈦回收率>95%,鈦棒成本降低30%;
電子束冷床熔煉:西部超導(dǎo)制備6N級鈦錠(O≤10ppm),疲勞壽命提升50%。
七、國內(nèi)外產(chǎn)業(yè)化對比
維度 | 中國(寶鈦/西部超導(dǎo)) | 國際(ATI/VSMPO) | 差距與突破 |
最大棒材直徑 | φ500mm | φ800mm(俄羅斯) | 尺寸小37.5% |
增材制造效率 | 16m2/120h(北航) | 20m2/96h(德國EOS) | 效率差25% |
超純鈦控制 | O≤100ppm(航空級) | O≤50ppm(美國ATI) | 純度差1倍 |
成本優(yōu)勢 | TC4棒材¥120/kg(鴻輝鈦) | Gr5棒材$35/kg | 價格低40% |
涂層壽命 | 5000h(WC-CrN) | 8000h(AlCrY/YSG) | 耐磨性差37.5% |
中國突破點:煜鼎增材實現(xiàn)16m2鈦框整體打印,材料消耗降80%;華鈦瑞翔鈦合金葉片量產(chǎn)成本降至$8000/片(國際$15000)。
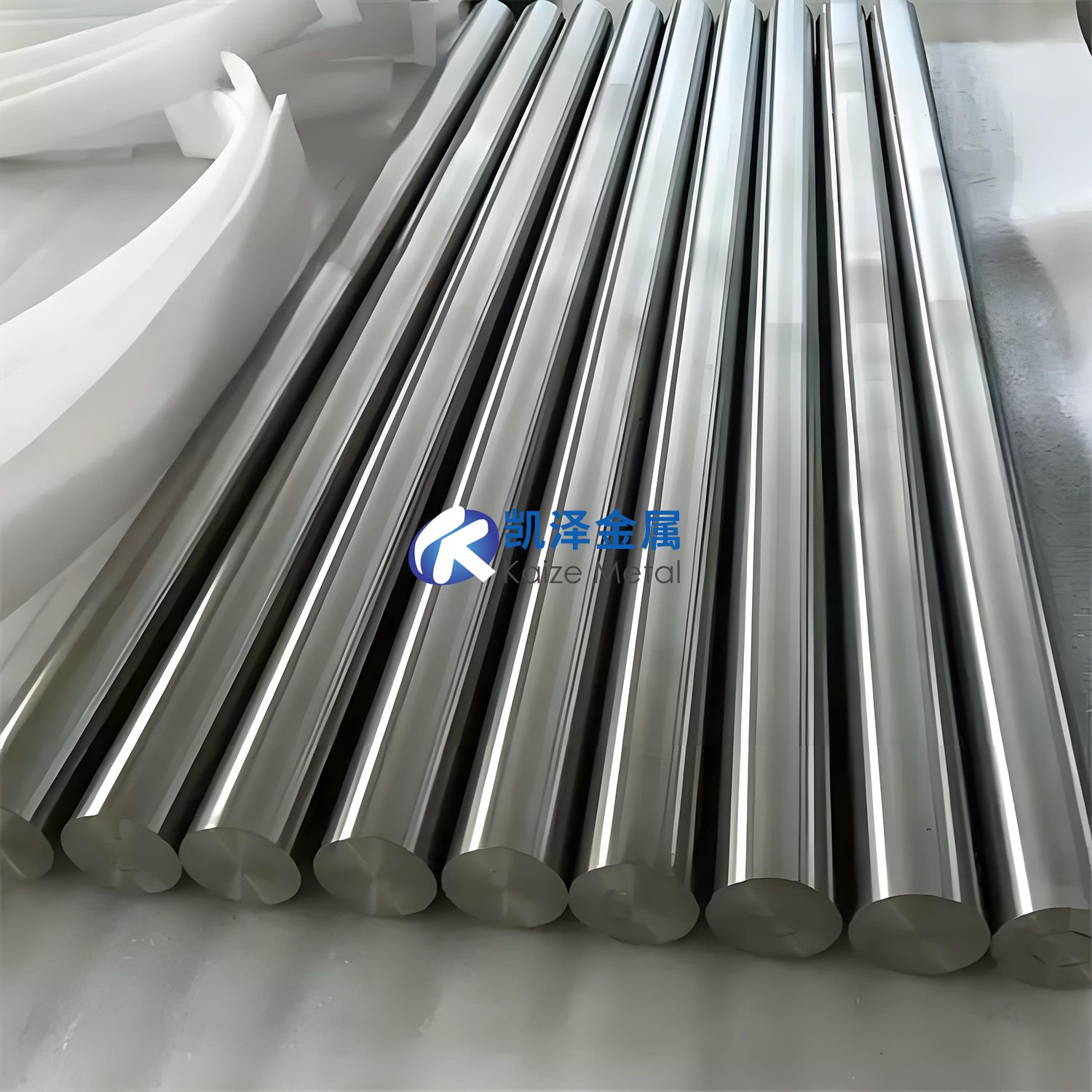
八、技術(shù)挑戰(zhàn)與前沿攻關(guān)
(1)耐磨性提升瓶頸
解決方案:
納米復(fù)合涂層:TiC-SiC納米線增強,硬度突破25GPa;
表面織構(gòu)化:激光微坑加工(直徑50μm,深20μm),儲油率提升70%。
(2)大規(guī)格棒材均質(zhì)化
創(chuàng)新工藝:
磁場輔助燒結(jié):哈工大開發(fā)3T強磁場,φ400mm棒材心部強度波動≤5%;
梯度熱處理:分區(qū)控溫(邊部780℃/心部820℃),消除殘余應(yīng)力90%。
九、趨勢展望
智能制造集成
機器學(xué)習(xí)優(yōu)化切削參數(shù):東芝AI模型預(yù)測刀具磨損誤差<5%,加工效率提升40%;
在線超聲監(jiān)測:實時反饋磨削燒傷,良品率提升至99.5%。
多材料復(fù)合結(jié)構(gòu)
鈦-陶瓷梯度齒輪:表面TiB?層(耐溫1000℃),基體TC4保持韌性,扭矩承載提升3倍;
CFRP-鈦 hybrid銷釘:碳纖維包覆鈦芯,減重60%且阻尼特性提升。
低成本化路徑
殘鈦循環(huán)利用:2025年HDH技術(shù)推動再生鈦占比>30%,成本降至¥80/kg;
近凈成形擴散焊:齒輪毛坯加工余量<5%,材料利用率從15%提至85%。
產(chǎn)業(yè)建議:建立“材料-設(shè)計-涂層-檢測”一體化平臺,推動航空鈦部件成本降至鋼制件1.5倍內(nèi);加速制定《航空鈦合金軸類件微動磨損評價》國家標(biāo)準(zhǔn)(參考AMS 4992D)。
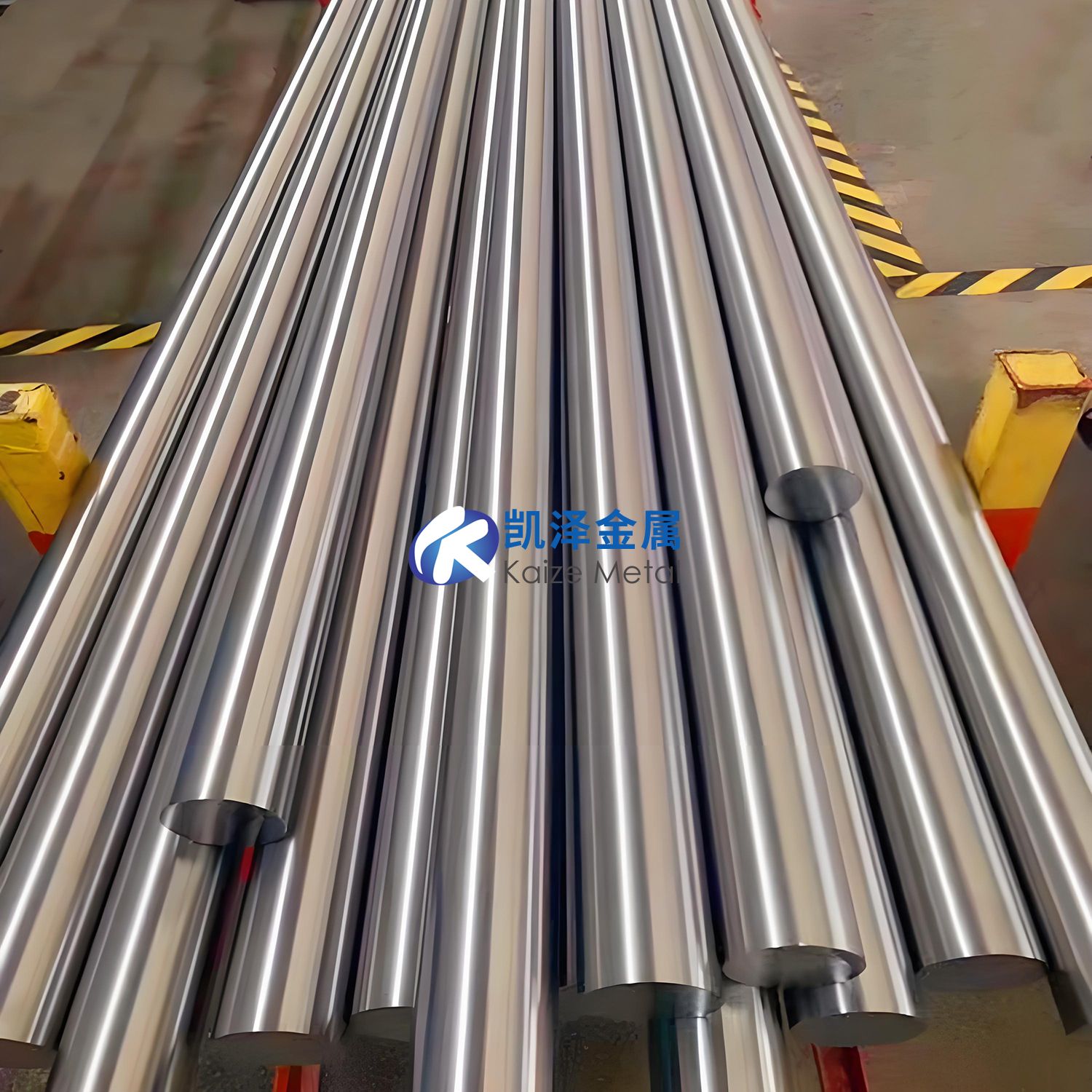
結(jié)語:
航空鈦棒正從“單一材料替代”向“結(jié)構(gòu)-功能一體化”躍遷,需在超細晶控制、智能加工及再生技術(shù)持續(xù)突破,支撐國產(chǎn)大飛機、深空探測器等高端裝備自主化。至2030年,增材制造鈦部件占比有望超40%,推動航空航天減重與壽命革命。
相關(guān)鏈接