鈦絲憑借成本與性能的雙重優勢,正成為大尺寸金屬3D打印的核心材料。未來需突破超大直徑絲材均質化(>Φ6mm)與多材料集成打印技術,同時通過NAMP等創新工藝釋放3D打印鈦合金的抗疲勞潛力,支撐航空航天、深海裝備的高可靠制造。以下是凱澤金屬涵蓋鈦絲材料特性、制備工藝、應用場景及前沿進展,將3D打印用鈦絲材料的系統性技術分析如下:
一、鈦絲在3D打印中的核心價值
鈦絲作為送絲式3D打印(如電子束熔絲沉積、電弧熔絲沉積)的關鍵原材料,具有以下不可替代的優勢:
成本效率:比鈦粉原料成本低40%~60%,且利用率高達95%(粉材利用率僅70%)。
性能優勢:
高強韌性:RT-1400鈦絲抗拉強度達1400–1600MPa,延伸率≥8%,適用于航空承力件。
低缺陷率:絲材經多道次拉拔,氣孔率<0.02%,顯著低于粉末打印的0.5%。
工藝適應性:直徑范圍覆蓋Φ0.8–5.0mm,兼容電子束(EBF)、電弧(WAAM)等主流送絲工藝。
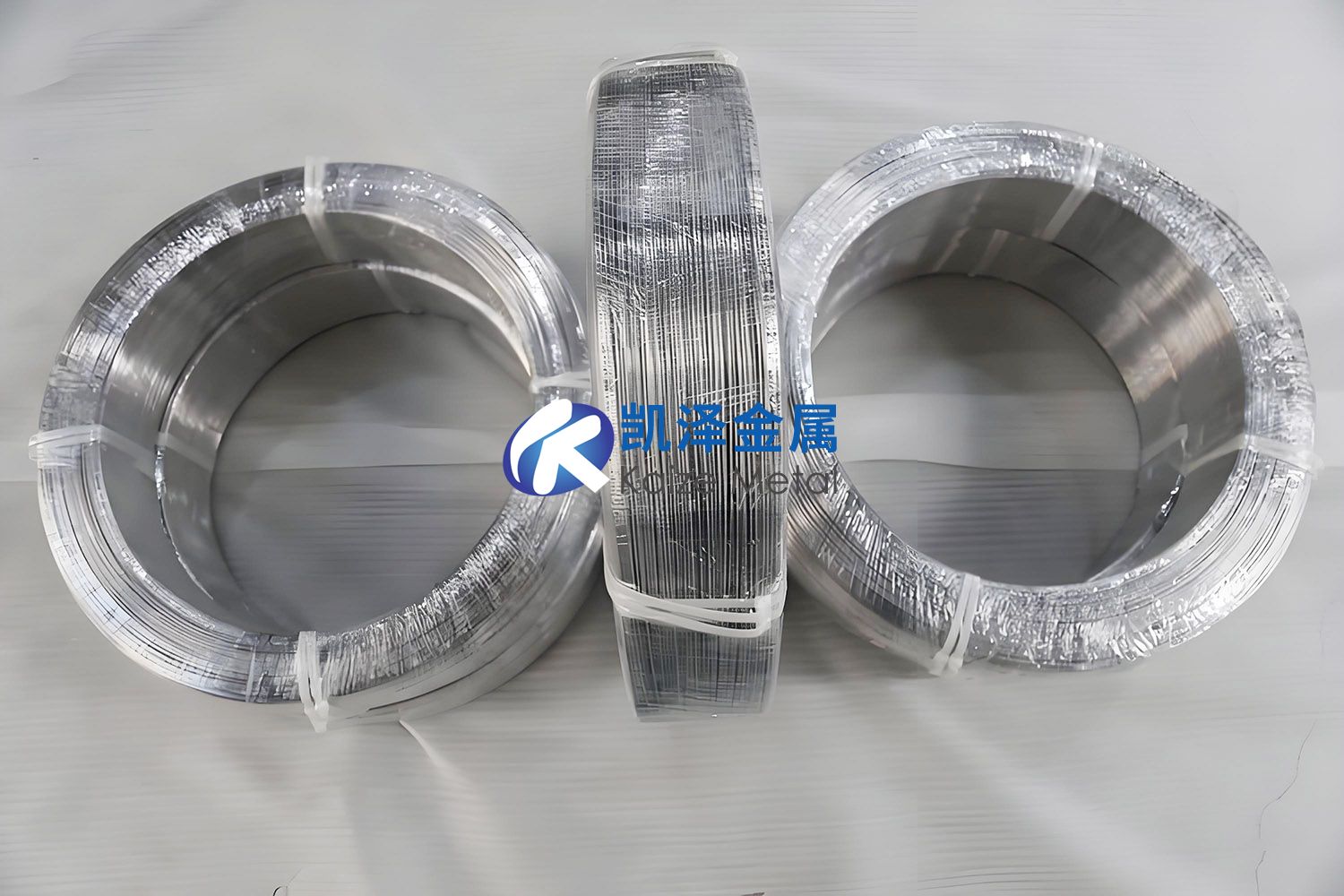
二、主流鈦絲材料類型與特性
(1)通用型鈦合金絲材
牌號 | 成分特點 | 力學性能 | 適用工藝 |
TC4 | Ti-6Al-4V(α+β雙相) | 抗拉強度895–1030MPa,延伸率≥10% | EBF、WAAM、激光熔覆 |
TA1 | 工業純鈦(低氧含量≤0.15%) | 抗拉強度500–650MPa,塑性優異 | 醫療植入物打印 |
RT-1400 | Ti-4.5Al-3V-1.5Cr-6Mo-Fe | 抗拉強度1400–1600MPa(高強韌) | 航天結構件 |
(2)特種功能化鈦絲
海洋工程用鈦絲:Ti-6Al-7Nb-2.6Zr-0.6Mo(O≤0.15%),抗拉強度≥780MPa,耐海水腐蝕率<0.001mm/a,用于船舶螺旋槳3D打印。
抗疲勞鈦絲:通過NAMP工藝(Net-Additive Manufacturing Process)消除微孔,疲勞強度達978MPa,比傳統打印件提升106%。
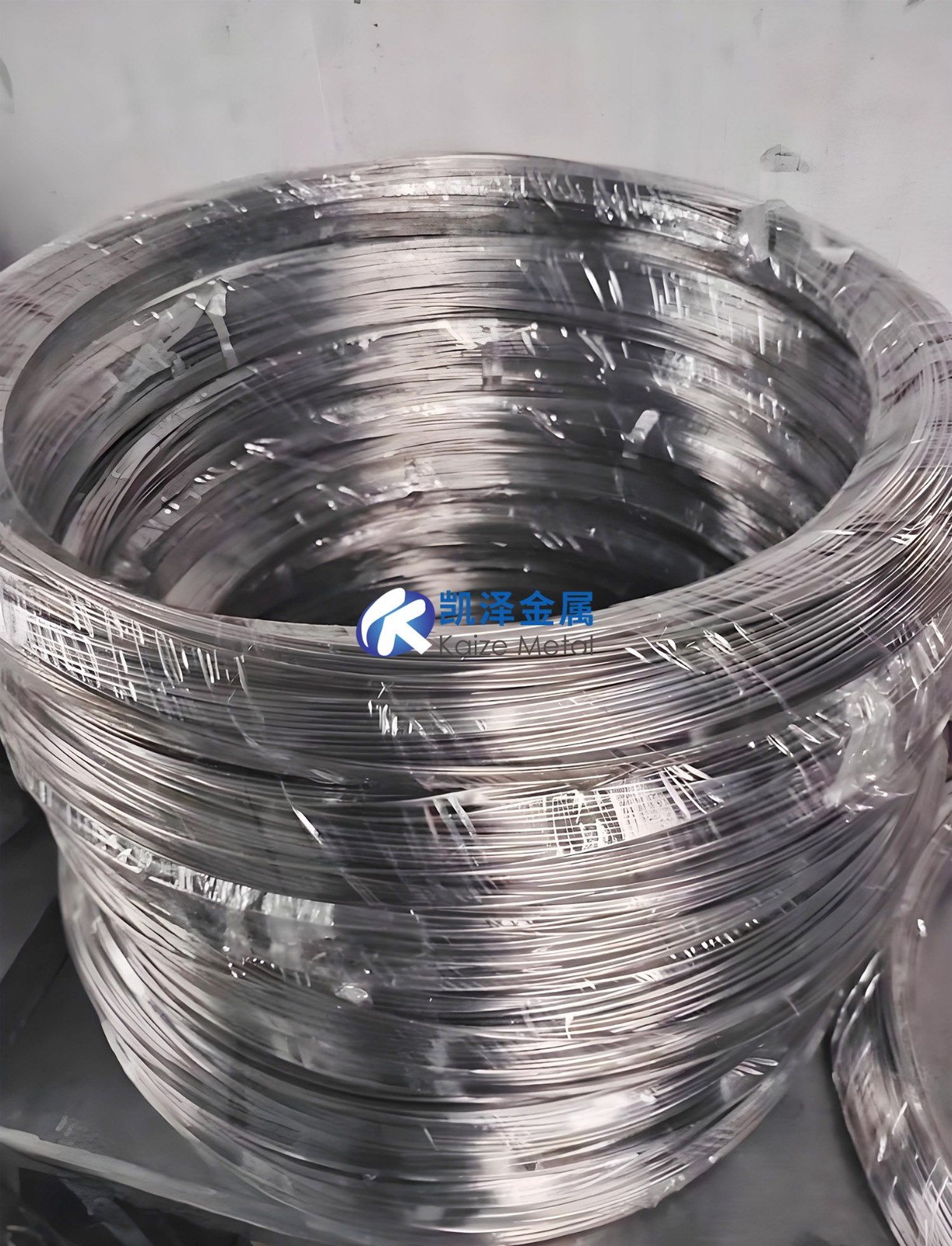
三、先進制備工藝與技術突破
1. 拉拔工藝創新
多段溫控拉拔:
RT-1400鈦絲采用三段熱拉拔(780–820℃),道次變形量從0.5mm→0.3mm→0.1mm階梯遞減,避免表面軟化。
慢速拉拔(常規速率50%)使心表硬度差≤9HV,屈服強度波動<5%。
輥模拉絲技術:結合異步軋制與在線氬氣保護,晶粒細化至2–5μm,延伸率提升至18%。
2. 表面處理革新
環保刮削工藝:替代酸洗/磨光,徹底去除表面雜質,焊接熔合率提升20%(邢臺余光焊材案例)。
超純熔煉:電子束冷床精煉(EBCHM)使氧含量≤10ppm,疲勞壽命提升50%。
3. 組織調控技術
全等軸晶制備:西北工業大學開發交替參數成形(APP),激光功率周期性切換(1200W?2400W),消除柱狀晶,各向異性<5%。
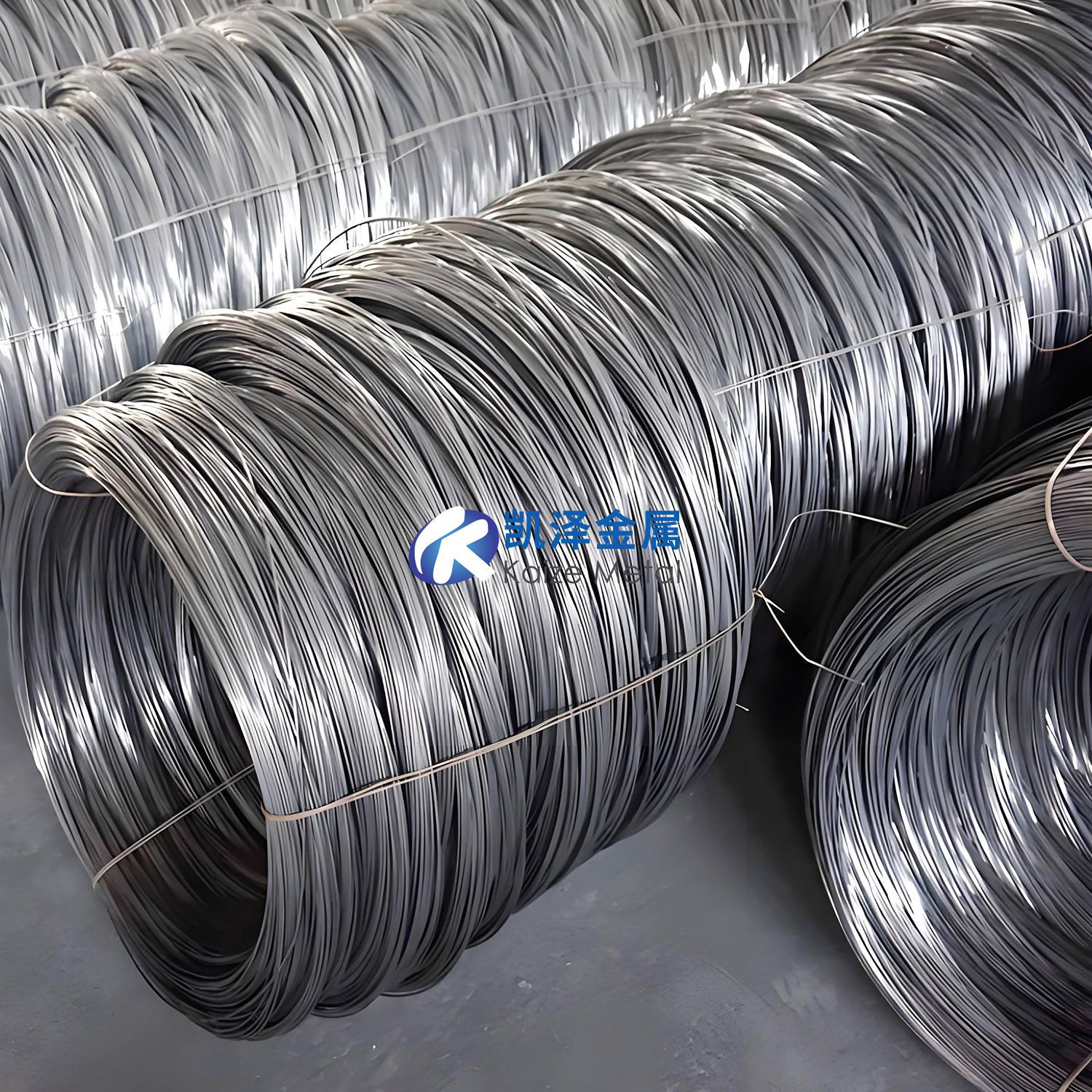
四、技術挑戰與解決方案
(1)屈服強度波動
問題:快速拉拔導致心部硬、表面軟,Φ5mm TC4絲材屈服強度僅780MPa(心部達918MPa)。
對策:
降低拉拔速度 + 分段變形控制(如RT-1400工藝)。
表面噴丸強化:產生785MPa壓應力,均勻化表層組織。
(2)大尺寸絲材均質化
磁場輔助燒結:哈工大開發3T強磁場,Φ400mm棒材心表強度差≤5%。
梯度熱處理:邊部780℃/心部820℃分區控溫,消除殘余應力90%。
五、應用案例與產業化現狀
(1)航空航天領域
CJ-1000A發動機:采用EBF打印TC11渦輪葉片,減重50%,耐溫750℃(傳統工藝650℃)。
SpaceX星艦定位銷:SLM成型鈦絲構件,抗剪切強度≥670MPa,減重45%。
(2)海洋工程領域
深海閥門組件:電子束熔絲打印Ti-6Al-7Nb-2.6Zr閥體,抗拉強度780MPa,耐壓能力達1500米水深。
(3)醫療植入物
定制人工關節:TA1鈦絲激光熔覆,孔隙率梯度設計(表層80%→內部20%),骨整合效率提高40%。
(4)產業化對比
指標 | 中國(凱澤金屬) | 國際(ATI/VSMPO) |
最大絲徑 | Φ5.0mm(盤絲) | Φ6.0mm(俄羅斯VSMPO) |
抗疲勞性能 | 978MPa(NAMP工藝) | 850MPa(美ATI) |
成本 | ¥120/kg(TC4) | $35/kg(美標Gr5) |
中國突破:凱澤金屬實現6N級鈦絲量產(O≤10ppm);邢臺余光焊材開發刮削工藝提升焊接質量。

六、未來趨勢
智能化制造:
機器學習優化拉拔參數(如東芝AI模型預測誤差<5%)。
在線超聲監測缺陷,良品率提升至99.5%。
復合結構打印:
鈦-碳纖維混合絲材:碳纖維包覆鈦芯,阻尼特性提升30%(2024年試驗階段)。
綠色循環技術:
殘鈦氫化脫氫(HDH)再生:回收率>95%,成本降至¥80/kg(2030年目標)。
相關鏈接