1、序言
鈦合金?高溫合金等難加工金屬材料是航空航天領域制造渦輪盤?葉片?機匣等航空發動機關鍵零部件重要的原材料之一 [1,2]?但隨著工業的快速進步,尤其是航空航天的快速發展,這些關鍵零部件通常服役在高溫高壓?交變循環載荷?潮濕等惡劣條件下,因而對關鍵零部件的服役性能提出了嚴格甚至是更為苛刻的要求?如何提升關鍵零部件服役壽命,實現鈦合金等金屬材料高質高效加工是當前亟需解決的一個重要研究課題?
零件制造精度是其服役壽命的重要保證,采用有效的加工方法是提高關鍵零部件服役壽命的一個重要前提?切削加工作為常見的加工方式,在機械加工領域具有舉足輕重的地位,因而在難加工金屬材料加工中也得到了較為廣泛的應用?但由于難加工金屬材料的優秀力學性能導致其在傳統的機械加工中往往表現出切削力大?切削溫度高?刀具磨損嚴重?加工表面完整性差等特點,導致材料加工效率低?精度不高,同時提高了加工成本 [3]?
超聲振動輔助加工 (UVAM) 是一種非傳統的加工方法,它利用換能器 (壓電陶瓷 / 磁致伸縮) 將高頻電能轉換為高頻機械振動能,并將其應用于加工過程,從而實現材料的超精密加工?與傳統加工方式相比,由于加工特性的變化,材料的去除機理也發生了根本性變化?超聲輔助加工是在切削加工中于工件和刀具之間附加超聲振動,可大幅度降低刀具與工件間摩擦力,從而減小切削力和切削熱,同時切削刃的超聲振動又可加速切屑的疲勞破壞,提高了斷屑效果 [4]?尤其是刀具的超聲振動加速度最大可達重力加速度的數萬倍,所產生的慣性力使切屑極難粘附于切削刃上,可避免積屑瘤的產生和刀具的黏著磨損,因此在航空航天金屬材料加工中具有得天獨厚的優勢 [5]?超聲切削加工不同因素對切削性能的影響如圖 1 所示?當前,超聲振動輔助切削加工已用于難加工金屬材料,并且取得了較好的加工效果?
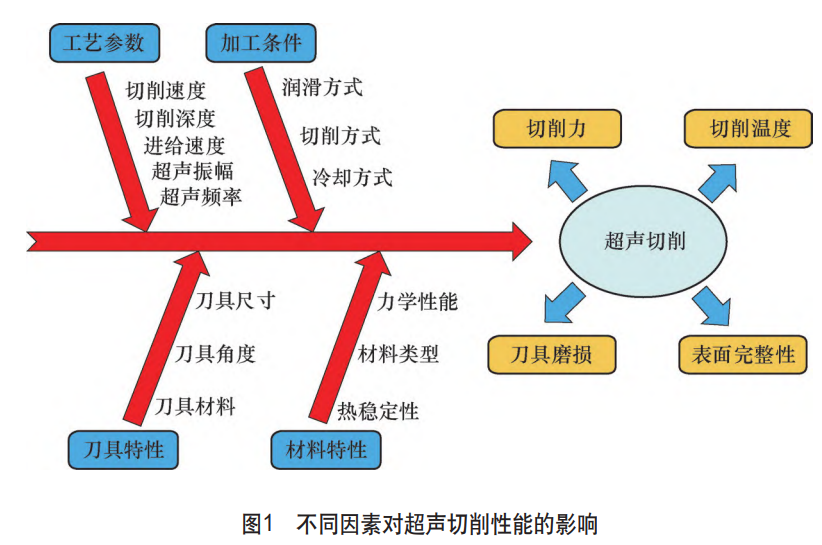
2、單一超聲切削加工研究現狀
2.1 切削力
傳統金屬切削加工過程中,刀具與工件間會發生嚴重的相互作用,因此會造成極大的切削力,對加工過程穩定性帶來極大的挑戰?因此一些學者采用超聲切削加工來減小切削力,提高加工過程穩定性?
切削力對刀具磨損和表面質量都有著重要的影響,SHEN 等 [6] 研究了超聲振動輔助立銑過程中銑削力的變化規律,結果表明超聲振動引起的分離現象會導致切削力曲線呈現脈沖式波動,并低于傳統銑削加工的平均切削力?SOFUO?LU 等 [7] 采用 DEFORM-2D 有限元軟件分別建立了鈦合金和哈式合金在普通車削?超聲振動輔助車削?熱超聲振動輔助車削三種加工過程中的有限元模型,分析了不同切削加工過程中的切削力,結果表明熱超聲振動輔助切削具有最低的切削力和有效應力?對于哈式合金,熱超聲振動輔助車削切削力降低了 50% 以上,而鈦合金切削力降低了約 70%, 這是因為熱超聲振動輔助切削加工具有熱軟化效應,降低了加工過程中的切削力,同時超聲加工中刀具與工件間的分離接觸現象可以進一步降低切削力?為了抑制鈦合金加工過程中的顫振,提高加工過程的穩定性,LANOS 等 [8] 采用超聲振動輔助車削對其進行加工,以材料去除率為目標,建立了基于工藝參數的切削力模型,并分析了不同加工參數對切削力的影響,結果表明相同參數下,超聲振動輔助車削可以獲得更小的切削力,從而抑制加工過程中產生的顫振現象?基于超聲銑削刀具運動軌跡,NIU 等 [9] 建立了縱扭超聲振動輔助銑削最大未變形切削厚度模型,在斜角切削模型和切削力幾何關系模型的基礎上,推導出了縱扭超聲振動條件下的銑削力模型,分析了刀具幾何參數和超聲加工參數對切削力的影響規律,結果表明預測值與試驗參數的變化規律相一致?在超聲加工參數中,縱扭相位差對兩個方向上的切削力影響最大,其次是超聲頻率和縱向振動振幅的影響,扭轉振幅的影響最小?WANG 等 [10] 基于刀具幾何形狀和刀尖切削運動軌跡建立了超聲條件下的銑削力預測模型,并得到了切削刃的瞬時切削厚度?結果表明縱扭超聲振動可以降低徑向切削力,而切向和軸向力沒有太大的變化,這主要與超聲的振動方向有關?為了提高表面加工質量,XU 等 [11] 分析了超聲條件下切削力的生成機理,建立了基于工藝參數條件下的超聲振動輔助車削 304 不銹鋼的切削力模型,結果表明超聲振動引入的分離效應可以極大降低加工過程中的切削力,但振幅不是越大越好,而是存在一個最佳值?通過合適的工藝參數匹配可以提高加工效果?NAMLU 等 [12] 用超聲振動輔助銑削和微量潤滑相結合的方式,探究了鈦合金銑削加工過程中各工藝參數對切削力的影響規律?無論何種冷卻方式,超聲條件下的切削力始終低于普通切削?同時發現切削力與加工階段有關,對應粗?精加工階段表現出不同的加工效果,在粗加工階段超聲切削可以有效降低切削力,而在精加工階段普通切削的切削力相對較低,因此最低切削力的理想組合是精切削中的微量潤滑 (MQL) 和常規銑削 (CM), 粗切削中的 MQL 和超聲輔助銑削 (UAM)?CHEN 等 [13] 通過全瞬態切削過程來分析超聲振動對加工過程的影響,考慮超聲振動對剪切區域剪切角和流動應力的影響,提出一種新的模型來確定平均切削力和瞬態切削力?結果表明超聲切削加工過程受瞬態特性?聲軟化?熱軟化?犁削和摩擦等多種特性的影響,Ti6Al4V?AISI 1045 和 Al6063 三種不同材料的切削力試驗值與預測值的誤差分別約為 7%?10.2% 和 11%, 超聲振動可以有效降低切削力?考慮振動對工件材料切削性能的影響,NIK 等 [14] 首先基于理論設計?有限元仿真?遺傳算法相結合的方式進行了超聲振動裝置的優化設計?在此基礎上,分析了不同加工參數變化對切削力和表面粗糙度的影響規律,發現超聲振動的施加可以減小切削力?改善表面質量?與普通磨削相比,超聲條件下的法向和切向磨削力分別降低了 13.5% 和 14.2%?王晨旭等 [15] 對 GH4169 高溫合金的超聲振動輔助磨削去除機理進行了研究,分析了加工參數對切削性能的影響規律,結果表明超聲振動顯著降低了加工過程中的切削力和砂輪磨損,同時表面質量顯著提高?
2.2 切削溫度
傳統金屬切削加工中,在切削接觸區域會產生極高的熱量,對刀具壽命和表面加工質量帶來不利影響?過高的切削溫度不僅使得刀具壽命急劇降低,而且造成加工表面產生粘附?甚至分層,因此采用超聲切削可以有效控制鈦合金的切削溫度,提高砂輪壽命和表面加工質量?不同切削方式下的切削溫度比較如圖 2 所示?
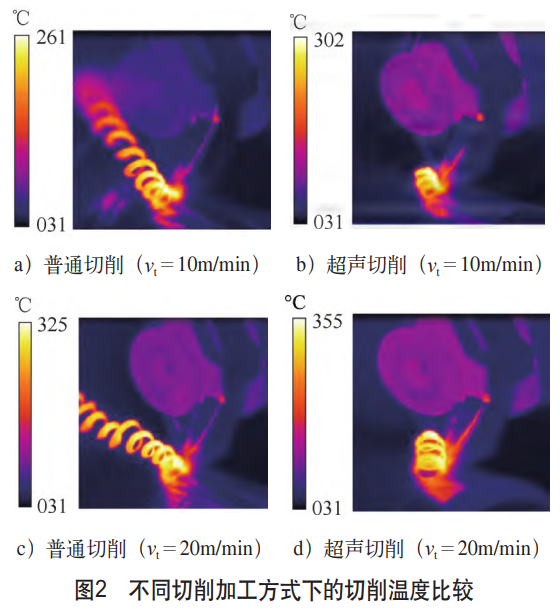
為了研究超聲振動對車削加工過程的影響,KHAJEHZADEH 等 [16] 采用 Al?O?涂層刀具對航空鋁材進行超聲輔助車削加工,研究了超聲振幅?切削速度和進給速度對切削溫度的影響,結果表明降溫效果與工藝參數的合理選擇有關,在小進給速度下提高超聲振幅可以有效降低切削溫度?LOTFI 等 [17] 采用有限元仿真分析了二維橢圓超聲振動對鎳基高溫合金切削加工性能的影響,結果發現橢圓振動的施加可以增大剪切角,減小前刀面的切削溫度,從而抑制切屑瘤的產生?基于非均勻移動熱源,CHEN 等 [18] 建立了鈦合金超聲輔助切削加工過程中的傳熱模型,分析了超聲振幅和頻率對加工傳熱過程的影響,結果表明等效熱源中心在刀具前刀面會傾向于向后移動,同時發現在水平和垂直方向上的溫度梯度并不一致?此外,計算了振動參數變化對平面和曲面加工中剪切面溫度的影響,發現超聲振幅和頻率的增加可以降低溫度梯度,從而導致剪切平面溫度降低,并且加工表面溫度隨著超聲振幅的增加而減小,而隨著頻率的增加卻呈現上升趨勢?LIN 等 [19] 發現最小微量潤滑和超聲振動的結合可以進一步改善單一超聲振動輔助車削的加工效果,顯著降低切削力?切削溫度?并且微量潤滑的效果與噴嘴的角度有關,通過有限元仿真分析了不同角度對切削溫度和應力變化的影響,結果表明合適的噴嘴角度有利于產生合適的冷卻?潤滑效果,提高表面加工質量并延長刀具使用壽命?考慮刀尖高頻正弦運動軌跡對加工過程的影響,GHOLAMZADEH 等 [20] 對干燥條件下的超聲振動輔助切削加工過程進行了二維有限元仿真,分析了加工相關參數對刀尖切削溫度的影響,結果表明某些狀態下刀尖的瞬時溫度高,但平均溫度相對較低,最高溫度發生在比刀尖位置略高的位置?為了探究鈦合金超聲振動輔助切削過程中耕犁效應對加工過程的影響,CHEN 等 [21] 采用有限元仿真分析了刀尖圓弧半徑對耕犁區應力狀態的影響,結果發現相比于傳統磨削,超聲振動會降低加工過程中的切削溫度,但切削溫度仍然會隨著切削速度和刀尖圓弧半徑的增加而增加,最大切削溫度出現在前刀面上,這是由于切削速度和刀尖圓弧半徑增加會導致切削能耗增加,刀具熱量通過切屑不斷在前刀面聚集而導致切削溫度升高?針對臨界切削速度對超聲切削加工效果的限制,ZHANG 等 [22] 提出了一種高速振動切削的加工方法來提高表面質量和加工效率,并建立了一種瞬態切削溫度模型來描述切削界面內加工溫度的變化,結果發現切削速度和占空比是影響切削溫度高低的主要因素,通常與加工參數的設置有關?為了預測加工參數對鈦合金切削性能的影響,MUHAMMAD 等 [23] 采用模糊邏輯模型預測了超聲振動輔助車削和傳統車削加工中工藝參數對切削溫度的影響,結果發現建立的模型對預測結果具有較高的精度,揭示了超聲振動切削降溫的內在機理?
2.3 刀具磨損
鈦合金等難加工金屬在傳統切削加工過程中會產生嚴重的力?熱負荷,從而造成刀具的快速磨損?刀具磨損過快不僅影響自身的使用壽命,而且對加工質量會產生顯著影響,并且會反過來進一步影響力?熱負荷的產生?不同切削加工方式對刀具磨損的影響如圖 3 所示?
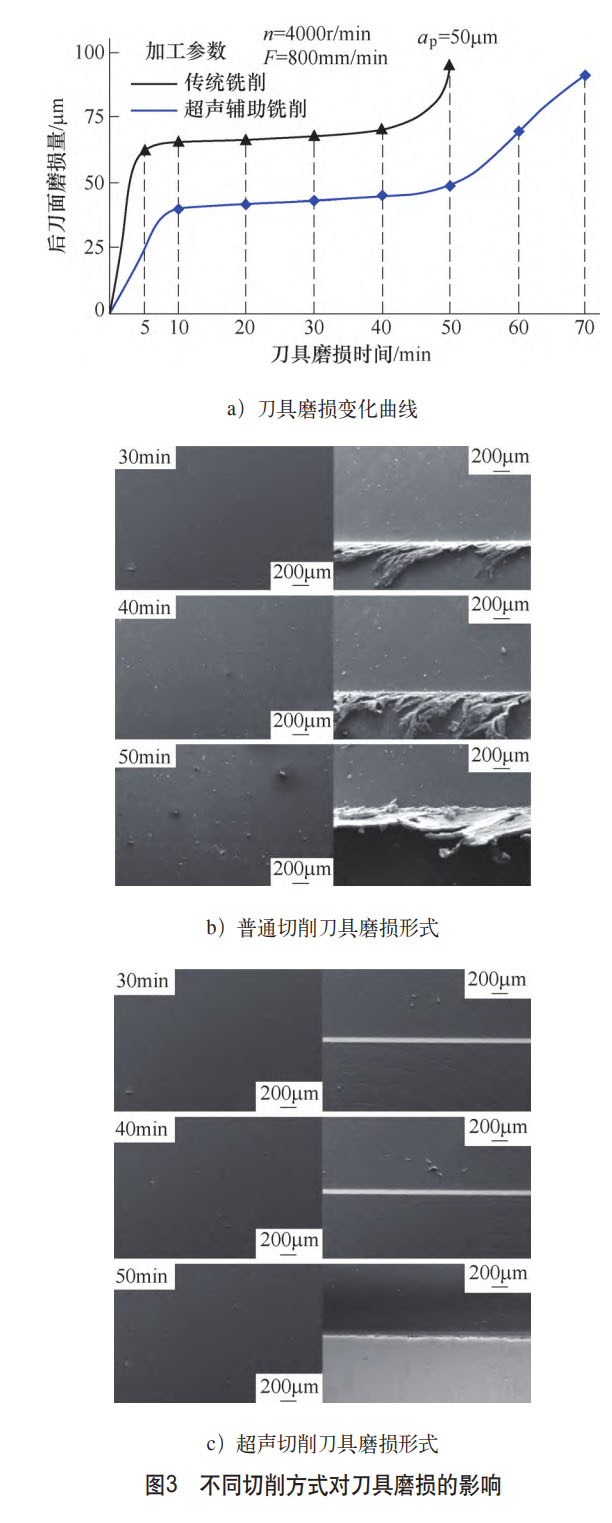
研究表明超聲振動可以有效降低刀具磨損?刀具磨損是鈦合金加工中的一個重要問題,NI 等 [24] 研究了超聲作用下刀具的磨損機理,分析了刀具不同磨損狀態對表面質量的影響,結果發現進給方向施加超聲振動后刀具主要有刀尖斷裂?裂紋等缺陷,這主要是由刀具與工件之間的高頻振動沖擊引起的,但相比于傳統銑削刀具的磨損程度明顯降低,并提高了加工表面質量?另外發現通過微量冷卻潤滑可以進一步改善加工效果?為了提高加工鈦合金時刀具的使用壽命,童景琳等 [25] 研究了縱扭超聲振動對銑削加工過程中刀具磨損特性的影響,結果表明縱扭超聲振動改變了刀具對工件的作用形式,從而減小了刀具的后刀面磨損,同時提高了表面加工質量?LIU 等 [26] 研究了超聲振動輔助銑削過程中刀具的磨損機理,研究表明超聲振動輔助銑削下的刀具存在著氧化磨損?黏結磨損?擴散磨損三種形式,刀具在正常磨損階段可以獲得最佳的表面加工質量?相對于普通銑削,相同條件下超聲振動輔助銑削刀具使用壽命長,并且加工表面質量更好,邊緣毛刺更加細小,同時切削力?切削溫度也都得到明顯的改善?YU 等 [27] 研究了橢圓超聲振動輔助車削過程中刀具的磨損機理,分析了有分離現象和無分離現象狀態下刀具磨損降低的內在原因,結果表明在無分離狀態的橢圓振動切削加工中,聲軟化效應降低材料屈服應力是降低刀具磨損的內在原因,而在有分離的條件下是刀具對工件的高頻沖擊降低了接觸應力,從而降低了刀具磨損?
2.4 表面質量
表面質量是影響工件疲勞壽命的一個重要指標,其加工質量的好壞直接決定工件的使用壽命?近年來,針對鈦合金等難加工金屬材料,為了改善其加工表面完整性,大量學者采用超聲振動輔助切削進行加工,獲得了良好的加工表面完整性?超聲對表面性能的影響如圖 4 所示?
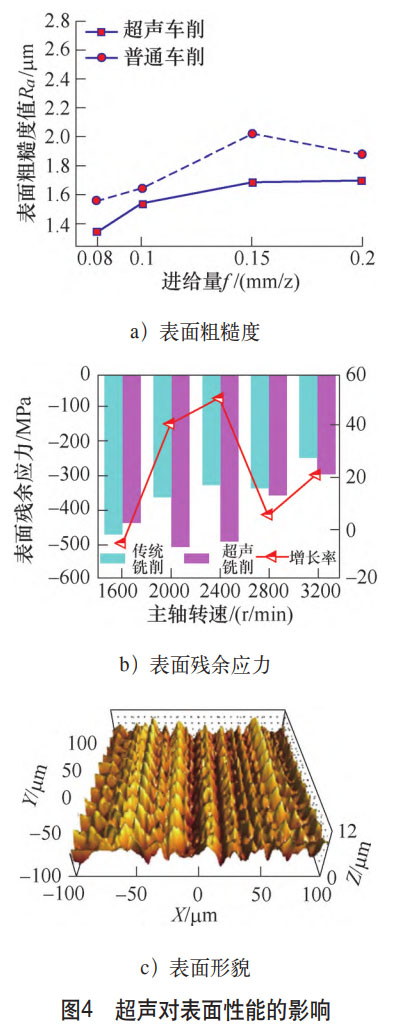
ZOU 等 [28] 對 304 奧氏體不銹鋼進行超聲振動輔助車削,分析了超聲振動對加工表面粗糙度的影響,結果發現合適的工藝參數匹配可以降低表面粗糙度值,提高表面加工質量?SUI 等 [29] 研究了超聲高速車削加工表面的形成機理,基于數值仿真和有限元模擬建立了表面形貌和表面粗糙度的預測模型,結果發現相比于常規切削,超聲高速切削能夠獲得更好的表面質量,表面粗糙度值可低于 0.4μm?考慮加工參數對 TC18 表面完整性的影響,XIE 等 [30] 采用超聲振動輔助銑削對其進行加工,分析了轉速和超聲振幅對表面完整性的影響,結果表明轉速對表面形貌以及殘余應力都有顯著的影響?與普通銑削加工表面形貌相比,超聲加工過后的表面微觀組織更加規則,切削表面殘余壓應力可增加 50.9%?超聲振動還可以使得加工表層產生塑性變形層,從而提高表層的硬度,提高其表面耐磨性,塑性變形層厚度隨著超聲振動的增加而增加?為了提高鈦合金加工表面的耐磨性,PENG 等 [31] 采用高速超聲振動輔助車削對鈦合金進行加工,通過對加工表面完整性進行表征,發現相比于傳統車削,超聲振動輔助車削加工表面粗糙度值明顯下降,同時表層塑性變形深度得到大幅度提升,出現了晶粒納米梯度層,從而提高了表面顯微硬度?此外,加工表面出現了高達 840MPa 的殘余壓應力?
3、超聲復合切削加工研究現狀
復合能場輔助切削加工是在單一能場輔助切削加工的基礎上進一步復合其他能場進行協同加工的方法,利用不同能場各自的優點來彌補單一能場輔助切削加工的缺點,進一步提高加工過程的穩定性,提升加工效率和質量?
3.1 超聲激光加工
DESWAL 等 [32] 開發了一種將超聲振動與激光工藝相結合的新型超聲復合激光輔助切削加工工藝,通過對 3003 鋁合金進行加工,對比分析了傳統切削加工?單一超聲振動輔助加工?單一激光加工對材料加工性能的影響,結果發現相對于其他加工方式,超聲激光復合輔助切削加工的表面粗糙度值低,切削力小,形成的切屑也更加光滑,這是因為復合加工工藝不僅具有超聲加工中刀具與工件間的接觸 - 分離現象,還含有激光加工的熱軟化效應,因而切削力小,形成的切屑也更加光滑?但在加工過程中發現超聲激光復合加工工藝具有最高的切削溫度,這是由于激光熱效應在刀具與工件分離的過程中熱能進一步聚焦到加工區域,導致切削過程中溫度最高?考慮超聲激光復合能場加工條件下對鈦合金銑削加工性能的影響,蘇永生等 [33] 分析了超聲激光復合能場對表面形貌?切削力?刀具磨損等性能指標的影響,結果表明普通銑削激光選區熔化鈦合金時,切削力隨著切削速度的增加而降低,隨進給速度的增加而升高,表面會出現明顯的刀痕,而超聲加工激光選區熔化鈦合金時則切削力相對較低,加工表面也較為光滑,這是因為激光對鈦合金金相組織的改變以及超聲加工中刀具與工件接觸 - 分離特性綜合作用的影響?此外發現在所選參數范圍內,超聲加工與普通加工激光選區熔化鈦合金刀具前后刀面都會產生嚴重的黏結現象,表明超聲改善刀具前后刀面的抗粘附性效果有限?合適的工藝參數對加工效果有著重要的影響,DOMINGUEZ 等 [34] 探究了激光 - 超聲復合加工中切削參數對切削力和表面粗糙度的影響,結果發現單一激光?超聲加工相比于傳統切削加工都能降低切削力?切削溫度,但都主要受限于較低的切削加工參數,而超聲 - 激光復合加工結合了超聲刀具 - 工件分離特性和激光熱軟化效應的雙重優點,加大了切削參數的使用范圍,可以進一步降低切削力和表面粗糙度值,同時還能提高加工效率?
3.2 超聲磁場加工
YIP 等 [35] 還將超聲能場與磁場相結合的方式來對鈦合金進行加工,在超聲波輔助金剛石切削中引入了磁場后,利用磁場對超聲加工的缺點進行彌補,最大限度地減少工具振動引起的表面損傷和側面毛刺,改善了鈦合金加工表面質量?試驗結果表明,在磁場存在的情況下,超聲刀具運動增強的材料溶脹程度顯著降低和抑制?由于磁場的影響,超聲波工具的循環運動引起的切割疤痕面積被最小化?此外,在磁場存在的情況下產生的凹槽深度和寬度的誤差百分比分別顯著降低到 1.69% 和 1.77%?圖 5 所示為不同加工方式對表面輪廓的影響?
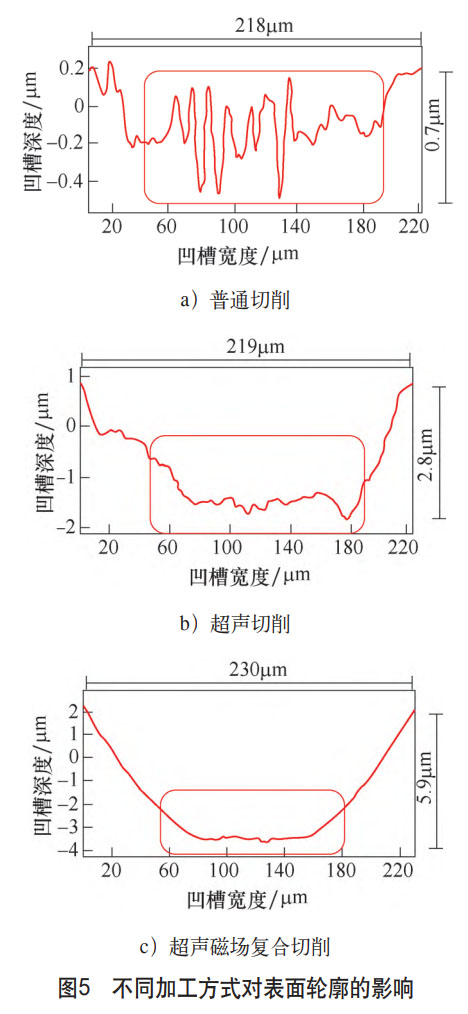
3.3 超聲電火花加工
DONG 等 [36] 基于超聲電火花加工 (UEDM) 加過程中的電壓變化,結合傳熱理論,建立了 TC4 鈦合金在單脈沖垂直超聲振動 UEDM 條件下的材料去除模型,并分析了不同振幅對材料去除過程的影響,結果表明超聲電火花輔助加工可以實現更高的材料去除率和表面質量?KURNIAWAN 等 [37] 對鈦合金進行超聲電火花輔助車削加工,采用有限元仿真分析了不同因素對加工過程的影響,結果表明電火花可以軟化工件材料,提高材料去除率,而超聲振動可以降低切削力?刀具磨損,同時抑制毛刺的產生?XU 等 [38] 利用其對鈦合金進行加工,并對比分析了電火花加工 (EDM)?超聲振動輔助銑削,結果表明超聲電火花輔助銑削加工具有超聲振動和電火花加工的雙重優點,電火花用于軟化待加工材料的表面,從而降低切削力,而超聲振動提高了電火花加工的放電效率,減小了切削力?與常規銑削 (CM)?超聲輔助加工 (USM)?電火花輔助加工 (EDAM) 相比,UEDM 具有更高的表面完整性,可以顯著抑制邊緣毛刺的產生?超聲電火花加工對切削性能的影響如圖 6 所示?
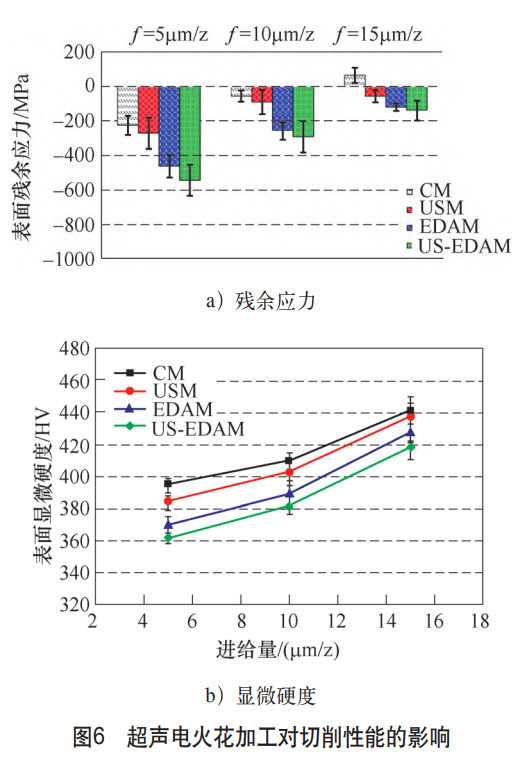
4、結束語
本文針對難加工金屬材料超聲切削加工研究現狀進行了總結,分析了超聲切削加工對難加工金屬材料切削性能的影響?研究表明超聲切削具有減小切削力?降低切削溫度?提高刀具壽命和加工表面完整性等優勢,但仍然存在一些問題與挑戰?針對當前難加工金屬材料超聲切削加工存在的問題與挑戰進行了展望,如下所述?
(1) 開發專用高精度振動切削機床 研制專用的主軸回轉精度高的振動切削機床,充分發揮振動切削的精密切削特性,將其應用于微納米加工領域?這將有助于進一步提升工件加工精度和表面質量,滿足高精度零件的加工需求?
(2) 推動超聲切削加工數控化和智能化 隨著數控技術的發展,將超聲切削加工技術應用于數控機床上,可以讓刀具獲得規律的運動方式,進一步提高加工精度?同時,結合人工智能技術,實現超聲切削加工的智能化控制,優化切削參數,提高加工效率和表面質量?這將有助于推動超聲切削加工技術在更廣泛的領域得到應用?
(3) 超聲切削加工標準的制定與完善 為了推動超聲切削加工技術的廣泛應用和規范化發展,需要制定和完善相關的技術標準和規范?這些標準和規范將涵蓋切削設備的性能要求?刀具的選擇和使用方法?切削參數的優化等方面,為超聲切削加工技術的標準化和規模化應用提供有力保障?
參考文獻:
[1] 趙彪,章敏秀,丁文鋒,等。單顆團聚 CBN 磨粒磨削 TC4 鈦合金表面創成機制 [J]. 表面技術,2023,52 (8):309–318.
[2] 武韓強,陳卓,葉曦珉,等。鈦合金超聲輔助等離子體氧化改性磨削基本加工特性研究 [J]. 機械工程學報,2024,60 (9):13–25.
[3] 張翔宇,路正惠,彭振龍,等。鈦合金的高質高效超聲振動切削加工 [J]. 機械工程學報,2021,57 (5):133–147.
[4] ZHAO M L,ZHU J M,SONG S J,et al. Influence of machining parameters in longitudinal-torsional ultrasonic vibration milling titanium alloy for milling force [J]. The International Journal of Advanced Manufacturing Technology,2022,123 (9): 3587–3597.
[5] 徐英帥,鄒平,王偉,等。超聲振動輔助車削高溫合金和鋁鎂合金研究 [J]. 東北大學學報 (自然科學版),2017,38 (1):95–100.
[6] SHEN X H,XU G F. Study of milling force variation in ultrasonic vibration-assisted end milling [J]. Materials and Manufacturing Processes,2018,33 (6):644-650.
[7] SOFUO?LU M A,?AKIR F H,GüRGEN S,et al. Numerical investigation of hot ultrasonic assisted turning of aviation alloys [J]. Journal of the Brazilian Society of Mechanical Sciences and Engineering, 2018,40:1-12.
[8] LANOS I,CAMPA á,ITURBE A,et al. Experimental analysis of cutting force reduction during ultrasonic assisted turning of Ti6Al4V [J]. Procedia CIRP,2018,77:86-89.
[9] NIU Y,JIAO F,ZHAO B,et al. Investigation of cutting force in longitudinal-torsional ultrasonic-assisted milling of Ti-6Al-4V [J]. Materials,2019, 12 (12):1955.
[10] WANG X B,JIAO F,ZHAO C Y,et al. Modeling and experimental analysis of cutting force in longitudinal–torsional ultrasonic-assisted milling of titanium [J]. Advances in Mechanical Engineering, 2019,11 (4):1687814019835107.
[11] XU Y S,WAN Z H,ZOU P,et al. Experimental study on cutting force in ultrasonic vibrationassisted turning of 304 austenitic stainless steel [J]. Proceedings of the Institution of Mechanical Engineers,Part B: Journal of Engineering Manufacture,2021,235 (3):494–513.
[12] NAMLU R H,SADIGH B L,KILI? S E. An experimental investigation on the effects of combined application of ultrasonic assisted milling (UAM) and minimum quantity lubrication (MQL) on cutting forces and surface roughness of Ti-6AL4V [J]. Machining Science and Technology,2021, 25 (5):738–775.
[13] CHEN X L,TANG J Y,SHAO W,et al. An analytical and experimental study on cutting characteristics and transient cutting frce modeling in feed directional ultrasonic vibration-assisted cutting of high strength alloys [J]. Materials,2022,15 (20):7388.
[14] NIK M G,MOVAHHEDY M R,Akbari J. Ultrasonic-assisted grinding of Ti6Al4V alloy [J]. Procedia Cirp, 2012,1:353–358.
[15] 王晨旭,徐念偉,張園,等。超聲輔助磨削 GH4169 高溫合金工藝研究 [J]. 電加工與模具,2022 (1):55–60.
[16] KHAJEHZADEH M,RAZFAR M R,AKHLAGHI M. Experimental investigation of tool temperature during ultrasonically assisted turning of aerospace aluminum [J]. Materials and Manufacturing Processes,2014,29 (11-12):1453–1460.
[17] LOTFI M,AMINI S. FE simulation of linear and elliptical ultrasonic vibrations in turning of Inconel 718 [J]. Proceedings of the Institution of Mechanical Engineers,Part E:Journal of Process Mechanical Engineering, 2018,232 (4):438–448.
[18] CHEN J B,XU M,XIE C,et al. A nonuniform moving heat source model for temperature simulation in ultrasonic-assisted cutting of titanium alloys [J]. The International Journal of Advanced Manufacturing Technology,2018,97:3009-3021.
[19] LIN J,WANG D. Effect of different nozzle angles on turning Inconel718 based on UEV [C]//2019 3rd International Conference on Electronic Information Technology and Computer Engineering (EITCE). IEEE,2019:896-899.
[20] GHOLAMZADEH B,SOLEIMANIMEHR H. Finite element modeling of ultrasonic-assisted turning: cutting force and heat generation [J]. Machining Science and Technology,2019,23 (6): 869-885.
[21] CHEN F Y,WANG D Z,WU S J. Influence of ultrasonic vibration-assisted cutting on ploughing effect in cutting Ti6Al4V [J]. Archives of Civil and Mechanical Engineering,2021,21:109.
[22] ZHANG X Y,PENG Z L,Liu L B. A transient cutting temperature prediction model for highspeed ultrasonic vibration turning [J]. Journal of Manufacturing Processes,2022,83:57-269.
[23] MUHAMMAD R. A fuzzy logic model for the analysis of ultrasonic vibration assisted turning and conventional turning of Ti-based alloy [J]. Materials,2021,14 (21):6572.
[24] NI C B,ZHU L D,YANG Z C. Comparative investigation of tool wear mechanism and corresponding machined surface characterization in feed-direction ultrasonic vibration assisted milling of Ti–6Al–4V from dynamic view [J]. Wear,2019, 436:203006.
[25] 童景琳,封志彬,焦鋒,等。超聲縱 - 扭復合銑削鈦合金刀具磨損特性研究 [J]. 表面技術,2019 (3): 297-303.
[26] LIU Q M,XU J K,YU H D. Experimental study of tool wear and its effects on cutting process of ultrasonic-assisted milling of Ti6Al4V [J]. The International Journal of Advanced Manufacturing Technology,2020,108:2917-2928.
[27] YU F H,ZHANG C,ZhU Q S,et al. Investigation of ultrasonic mechanism and development of tool wear model in ultrasonic elliptic vibration assisted cutting of stainless steel [J]. Tribology International, 2023,189:108962.
[28] ZOU P,XU Y,HE Y,et al. Experimental investigation of ultrasonic vibration assisted turning of 304 austenitic stainless steel [J]. Shock and Vibration,2015 (1):817598.
[29] SUI H,ZHANG X Y,ZHANG D Y. Surface modeling and analysis of high-speed ultrasonic vibration cutting [J]. Machining Science and Technology,2021,25 (1):100–117.
[30] XIE W B,WANG X K,LIU E B,et al. Research on cutting force and surface integrity of TC18 titanium alloy by longitudinal ultrasonic vibration assisted milling [J]. The International Journal of Advanced Manufacturing Technology,2022,119 (7/8):1-11.
[31] PENG Z L,ZHANG X Y,LIU L B,et al. Effect of high-speed ultrasonic vibration cutting on the microstructure, surface integrity, and wear behavior of titanium alloy [J]. Journal of Materials Research and Technology, 2023, 24:3870-3888.
[32] DESWAL N,KANT R. Hybrid turning process by interacting ultrasonic vibration and laser energies [J]. Materials and Manufacturing Processes, 2023, 38 (5): 570-576.
[33] 蘇永生,李亮,鐘相強。激光選區熔化鈦合金超聲輔助銑削性能研究 [J]. 表面技術,2022,51 (10): 321-327.
[34] DOMINGUEZ C J,AYVAR Soberanis S,KIMJ,et al. Hybrid simultaneous laser-and ultrasonicassisted machining of Ti-6Al-4V alloy [J]. The International Journal of Advanced Manufacturing Technology,2023,125 (3-4):1903-1916.
[35] YIP W S,TO S,SUN Z W. Hybrid ultrasonic vibration and magnetic field assisted diamond cutting of titanium alloys [J]. Journal of Manufacturing Processes,2021,62:743-752.
[36] DONG Y H,LIU J J,LI G Y,et al. Thermodynamic simulation modeling analysis and experimental research of vertical ultrasonic vibration assisted EDM [J]. The International Journal of Advanced Manufacturing Technology,2022,119 (7-8): 5303-5314.
[37] KURNIAWAN R,XU M,Li C P,et al. Numerical analysis in ultrasonic elliptical vibration cutting (UEVC) combined with electrical discharge assistance (EDA) for Ti6Al4V [J]. The International Journal of Advanced Manufacturing Technology, 2022,120 (1-2):471-498.
[38] XU M R,LI C P,KURNIAWAN R,et al. Ultrasonic and electrical discharge–assisted milling of the Ti-6Al-4V alloy [J]. The International Journal of Advanced Manufacturing Technology,2022, 122 (3-4):1897-1917.
相關鏈接