鈦合金是以Ti為主要成分的合金,并含鋁、釩、鐵和錳等元素以提高其性能。根據(jù)相組成不同,鈦合金可分為α鈦合金、β鈦合金和α–β鈦合金。其中α–β鈦合金 (如 Ti-6Al-4V)綜合性能良好,應(yīng)用最為廣泛。
鈦合金被認(rèn)為是“輕質(zhì)、高強、耐熱”材料的典型代表。它的強度高于鋼,密度卻僅約為其60%,并可長期服役于300~350℃的溫度環(huán)境,加之不同型號鈦合金展現(xiàn)出的在成形和焊接等方面的工藝特點,使鈦合金廣泛應(yīng)用于工程領(lǐng)域。最具代表性的是航空航天領(lǐng)域:航空發(fā)動機的風(fēng)扇葉片和低壓壓氣機/部分高壓壓氣機的葉片/葉輪/葉盤/機匣、航天飛行器的燃料儲箱和火箭發(fā)動機的外殼等重要零部件多采用鈦合金制造。在汽車行業(yè),采用鈦合金制成的發(fā)動機氣門/連桿和排氣系統(tǒng)等零部件對車身減重、發(fā)動機降噪具有重要意義。得益于突出的生物相容性,鈦合金也成為人體植入物和骨骼修復(fù)的首選金屬材料。
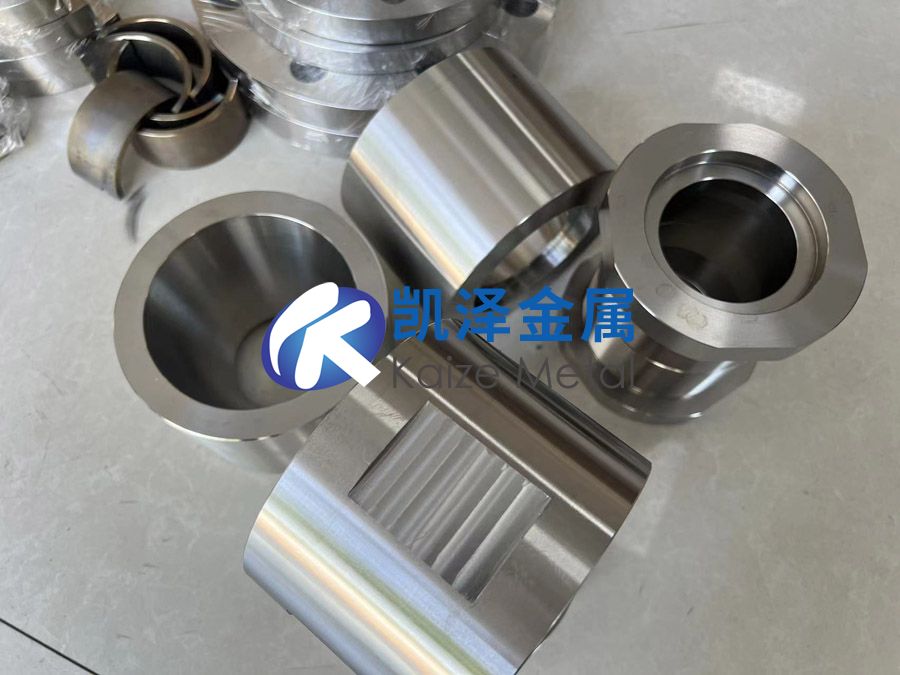
然而,由于強度高、導(dǎo)熱系數(shù)低和化學(xué)活性高等特點,鈦合金的機械加工難度較大,面臨加工效率低、工具磨損快、加工質(zhì)量差等問題。中外學(xué)者對此展開了一系列研究,探討了各典型工藝條件下的鈦合金加工件切/磨 削加工特點以及各類工具的應(yīng)用效果等。通過這些研究,已基本可以形成對鈦加工件切/磨削加工特點的較為全面和深入的了解。本文將結(jié)合上述方面分析鈦合金的切/磨削研究進展。
1、鈦合金切削/磨削加工存在的主要問題
1)切/磨削溫度高。鈦合金的強度高、熱強性好,因此在切/磨削過程中會產(chǎn)生大量熱量。然而,鈦合金的熱導(dǎo)率(低于7 W/(m·K))遠(yuǎn)低于鋼和鋁合金的;在切/磨削過程中,除部分熱量可通過切/磨屑、切削液和刀具/磨具傳導(dǎo)外,其余熱量中僅少數(shù)可及時傳導(dǎo)至 工件內(nèi)部,導(dǎo)致大量切/磨削熱聚積在接觸區(qū)。這一方面加快了工具磨損速度,另一方面使工件表面熱影響層變厚,降低零件的力學(xué)性能。有時不得不降低加工效率以減弱聚積熱量的不利影響。
2)工件材料彈性變形大。鈦合金的彈性模量較低,因此在其切/磨削過程中彈性變形較大,制約了加工精度特別是薄壁件加工精度。此外,工件材料的彈性變形和恢復(fù)是切削振動的重要誘因。工件材料彈性變形大,則工件材料和刀具/磨粒的接觸面積增大,導(dǎo)致刀具/磨粒的后刀面磨損嚴(yán)重。
3)工具黏附現(xiàn)象嚴(yán)重。鈦合金的塑性良好,切削刃和工件材料在接觸壓強的作用下易產(chǎn)生“冷焊”現(xiàn)象,造成工件材料黏附。另外,鈦合金的化學(xué)活性高,鈦元素在切/磨削溫度的作用下易與工具材料中的碳、 氮等元素以及空氣中的氧元素等發(fā)生化學(xué)反應(yīng),加劇工具與工件材料之間的黏附傾向。黏附的工件材料在剝離時會導(dǎo)致少量刀具/磨粒材料一同脫落。嚴(yán)重的黏附現(xiàn)象是導(dǎo)致切/磨削加工鈦合金時工具磨損快的金剛石與磨料磨具工程 總第239期主要原因之一。
2、鈦合金切削加工技術(shù)研究進展
2.1 鈦合金的切削加工性
在相同工藝條件下(切削速度100~180m/min, 干切),Ti-6Al-4V 和正火45鋼的車削加工的主切削力相當(dāng),前者對應(yīng)的徑向切削力高15%~30%,切削溫度(700~800℃)高約7%。相比之下,濕式切削(5%的乳化液)可使切削力降低約10%,切削溫度降 低約5%,同時表面質(zhì)量也得以改善。
為獲得良好的表面完整性,應(yīng)合理選擇切削用量。總體而言,切削速度越高,表面硬化越嚴(yán)重;進給速度 則對硬化程度無顯著影響。切削速度、切深和進給速度的增大均可導(dǎo)致表面粗糙度增大。切削表面易產(chǎn)生 一定程度的殘余拉應(yīng)力,亞表面則多為殘余壓應(yīng)力;增大進給和切深,表面的拉應(yīng)力水平和亞表面的壓應(yīng)力水平越高。出于切削溫度考慮,一般應(yīng)選用較低的切削速度和較大的切深,同時選用適配的切削液。
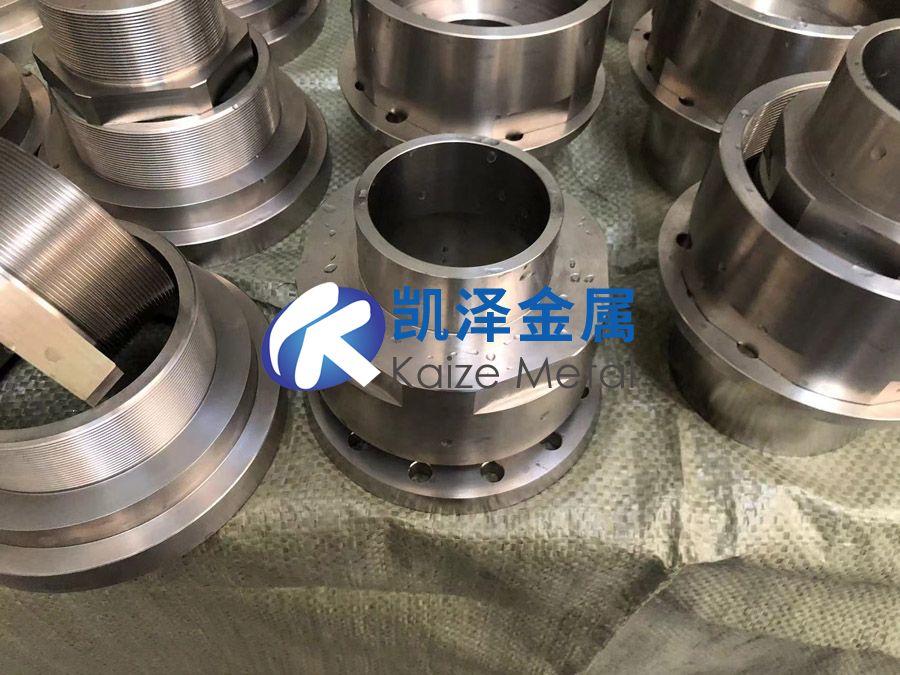
2.2 鈦合金切削刀具選擇
切削高溫等引起的刀具快速磨損是鈦合金切削過程存在的主要問題。因此,開發(fā)鈦合金切削專用的高性能刀具是未來需要研究的重要課題。
加工鈦合金時,涂層硬質(zhì)合金刀具和聚晶金剛石(PCD)刀具顯示出優(yōu)異的切削性能,尤以PCD刀具為最佳;聚晶立方氮化硼(PCBN)刀具次之;TiC基硬質(zhì)合金刀具和陶瓷刀具因耐用度低等原因被認(rèn)為不適用于鈦合金切削加工。PCD刀具與鈦合金切削的高匹配性主要源自其良好的導(dǎo)熱性和極高的硬度:金剛石的導(dǎo)熱系數(shù)為硬質(zhì)合金的數(shù)倍,更多切削熱可通過刀具傳導(dǎo)出切削區(qū);極高的硬度則保證了刀具的耐磨性。采用PCD刀具切削鈦合金的刀具耐用度可達(dá)硬質(zhì)合金刀具的數(shù)十倍。未來應(yīng)從刀具制備(焊接、切割和刃磨等)和切削工藝優(yōu)選(切削用量選擇和切削液供給等)等方面入手,降低PCD刀具切削鈦合金的刀具成本,進一步擴大其應(yīng)用范圍。
刀具角度方面,一般選擇較小的前角切削鈦合金,以增大切屑與前刀面的接觸長度;同時選擇較大的后角,以減小后刀面與加工表面之間的摩擦。
2.3 鈦合金高速切削技術(shù)
高速切削的主要特征是在常規(guī)切削的基礎(chǔ)上大幅提高切削速度。“高速”是一個相對概念,具體值取決于工件材料的力學(xué)性能等。對鈦合金而言,一般切削速度超過100 m/min即可認(rèn)定為高速切削。高速切削具有以下優(yōu)勢:
(1)加工效率高。高速切削一般同時采用高主軸轉(zhuǎn)速和快進給速度,從而使材料去除率成倍提高,最高可達(dá)常規(guī)切削的5倍甚至更高。
(2)可提高工件表面質(zhì)量和加工精度。高速切削時,由于剪切變形區(qū)變窄等因素,切削力小于常規(guī)切削時的切削力,有利于保證零件尤其是薄壁件的加工精 度;同時,大部分切削熱被切屑帶走,傳入工件的熱量比例較低,有助于提高其表面質(zhì)量和加工精度。
(3)刀具相對壽命長。在高速切削條件下,雖然刀具的使用時長有所下降,但切削效率的提升更為明顯, 即等量的刀具磨損可完成更多的切削任務(wù)。換言之, 刀具的相對壽命得到提升。
(4)高切削速度條件下,切削過程產(chǎn)熱增多。這對 機床的冷卻系統(tǒng)以及刀具的耐磨性和熱強性等是一個挑戰(zhàn)。此外,高速切削還要求機床具有較高的剛度和精度等,以充分發(fā)揮其工藝優(yōu)勢。目前美、日、德等國 在上述方面的發(fā)展水平處于領(lǐng)先位置。
3、鈦合金磨削加工技術(shù)研究進展
3.1 鈦合金的磨削加工性
磨削溫度高、磨削力大是鈦合金磨削加工的顯著特點。在普通磨削條件下,Ti-6Al-4V 對應(yīng)的磨削力約為45鋼的1.5~2倍,磨削溫度高約20%~30%,即使采用導(dǎo)熱性好的CBN 磨 料,磨 削 溫 度 亦 高 達(dá) 400℃。若采用緩進深切工藝磨削鈦合金,切削液難以充 分冷卻整個磨削弧區(qū),應(yīng)格外注意磨削溫度控制。
不同于切削,磨削依靠眾多磨刃的微切削作用去除材料,并且為負(fù)前角切削,因此工件材料在磨粒的擠壓和切削等作用下變形較為劇烈,導(dǎo)致磨削表面往往存在較為嚴(yán)重的魚鱗狀涂覆等現(xiàn)象。提高磨削速度可通過降低單顆磨粒切厚顯著改善這一問題。在普通磨削條件下,由于磨削溫度較高,磨削后工件表層多為殘余拉應(yīng)力。例如,采用SiC砂輪在普通磨削條件下加工Ti-6Al-4V時,磨削表面的殘余拉應(yīng)力高達(dá)500MPa以上。若采用緩進深切磨削工藝,正常磨削時弧區(qū)溫度僅約為100℃。此時磨削力在殘余應(yīng)力的形成過程中起主導(dǎo)作用,因此表面多為殘余壓應(yīng)力。
3.2 鈦合金磨削砂輪選擇
在普通磨料中,SiC磨料與鈦合金間的親和性較低,因此其磨削效果優(yōu)于剛玉磨料的。若采用剛玉磨料磨削鈦合金,為避免砂輪表面產(chǎn)生大規(guī)模的材料黏 附,須將磨削速度控制在約10m/s。在現(xiàn)有磨具技術(shù)2第5期徐九華:鈦合金切削磨削加工技術(shù)研究進展水平下,普通砂輪磨削鈦合金時砂輪磨損速度較快。例如,采用SiC砂輪在普通磨削條件下加工鈦合金的磨削比僅約為1。選用超硬砂輪時則提升幾十甚至上百倍。此外,相對于普通磨料,超硬磨料的導(dǎo)熱能力顯著增強,因此可以獲得較高的材料去除率。另一方面, 采用超硬砂輪磨削鈦合金時可以避免頻繁地修整砂輪,進一步提高磨削加工效率。
即便如此,在工程實踐中,仍多采用普通砂輪加工鈦合金。制約超硬砂輪廣泛應(yīng)用的原因主要有:(1)砂輪價格昂貴,導(dǎo)致加工成本顯著高于用普通磨料砂輪 磨削的成本;(2)砂輪修整難度大。因此,后續(xù)研究可重點關(guān)注超硬砂輪的制備與修整技術(shù)。
3.3 鈦合金磨削溫度控制技術(shù)
磨削高溫是抑制鈦合金磨削加工效率的重要原因。對此研究人員從開發(fā)新型磨具和改善冷卻方式等方面進行了一系列研究,取得了顯著效果。
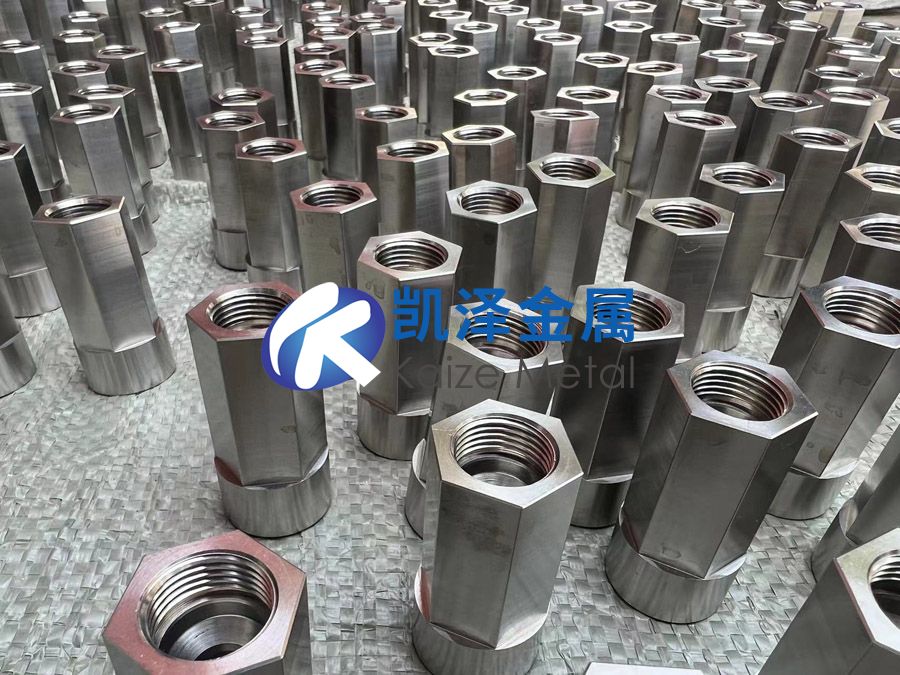
南京航空航天大學(xué)徐九華團隊將超硬磨料釬焊技術(shù)與磨粒有序排布技術(shù)相結(jié)合,開發(fā)出磨粒有序排布 釬焊CBN砂輪。該種砂輪磨粒出露高,可提供充足的容屑空間,從而減少磨削(特別是高效磨削)過程中砂輪與工件之間的摩擦。在此基礎(chǔ)上進一步開發(fā)了開槽釬焊 CBN 砂輪,可使更多切削液進入磨削弧區(qū)。該型砂輪在降低鈦合金磨削溫度方面顯示出明顯優(yōu)勢,在大切深的磨削條件下該優(yōu)勢更為明顯。在改善冷卻方面,主要有熱管砂輪技術(shù)、低溫冷風(fēng)技術(shù)和徑向水射流技術(shù)等。例如,熱管砂輪技術(shù)基于內(nèi)冷卻的角度實現(xiàn)對磨削弧區(qū)的強化換熱,弧區(qū)熱量經(jīng)熱管迅速疏導(dǎo),以達(dá)到少用或不用切削液的目的;在微量潤滑磨削時采用低溫冷風(fēng)技術(shù),可以顯著改善磨削弧區(qū)的換熱狀況,同時可以降低砂輪黏附程度。
4、TiAl合金切削/磨削加工技術(shù)研究進展
TiAl合金是一類特殊的高溫鈦合金。它的服役溫度比普通鈦合金的服役溫度高200℃以上,因此擁有廣闊的應(yīng)用前景。TiAl合金共有4種形態(tài):α2–Ti3Al、γ–TiAl、TiAl3和Ti2AlNb;其中,γ–TiAl因優(yōu)異的綜合性能得到了廣泛研究。針對該合金的制備方法和材料特性的研究已較為成熟,針對其切/磨削性能有若干研究,現(xiàn)結(jié)合其主要材料特點介紹如下。
與普通鈦合金相比,γ–TiAl的塑性較差(室溫延 伸率≤2%)。因此,在其切削加工過程中,局部材料可能發(fā)生脆性斷裂,在切削表面形成材料剝離和裂紋。根據(jù)車削表面的材料剝離和裂紋的形態(tài)推測,層片狀顯微結(jié)構(gòu)是引起上述表面缺陷的內(nèi)因:片狀晶粒之間的晶界在切削力熱的耦合作用下萌生微裂紋并延伸至 一定深度,最終導(dǎo)致局部材料被從工件表層“拔出”。磨削的單顆磨粒切厚遠(yuǎn)小于切削加工的切厚,磨削表面不存在嚴(yán)重的材料剝離和裂紋現(xiàn)象。另外,γ–TiAl的強度低于普通鈦合金的,并且由于鋁元素含量較高 (原子數(shù)占比一般為42%~48%),材料的導(dǎo)熱系數(shù)有所提升。這對于其切/磨削加工性而言是利好因素。例如,在同一磨削用量水平下磨削加工 γ–TiAl和 Ti-6Al-4V,前者的磨削比能低,磨削比也顯著更高。
5、鈦基復(fù)合材料切削/磨削加工技術(shù)研究進展
鈦基復(fù)合材料是指在純鈦或鈦合金中添加/原位生成硬質(zhì)增強相而形成的金屬基復(fù)合材料,在某些應(yīng)用場合也稱為高溫鈦合金材料。它具有比普通鈦合金更高的強度、比模量和更好的抗蠕變性能等,未來有望在航空工業(yè)、汽車、船舶等領(lǐng)域獲得廣泛應(yīng)用。
針對鈦基復(fù)合材料切/磨削加工的研究,多集中于擁有良好綜合性能的原位生成顆粒增強(TiC 等)的Ti-6Al-4V 基復(fù)合材料。結(jié)果表明,材料強度的提高以及增強相的存在提高了鈦基復(fù)合材料的切/磨削加 工難度。用 PCD刀具切削鈦基復(fù)合材料時,刀具磨粒磨損嚴(yán)重;切削Ti-6Al-4V 時刀具則以黏結(jié)磨損和擴散磨損為主。這可導(dǎo)致刀具耐用度相差數(shù)倍甚至數(shù)十倍。磨削時,鈦基復(fù)合材料對應(yīng)的磨削力高10%~20%,磨削溫度高約10%。
不同于鋁基復(fù)合材料,限于當(dāng)前材料制備技術(shù)的發(fā)展水平,已有研究涉及的鈦基復(fù)合材料增強相體積分?jǐn)?shù)集中于5%~10%。增強相體積分?jǐn)?shù)對材料的切/磨削加工性能存在顯著影響,體積分?jǐn)?shù)越高,切/磨削加工難度越大。因此,在實際應(yīng)用中,應(yīng)結(jié)合服役環(huán)境對材料性能的要求和切/磨削加工成本等因素綜合考慮,做出合理的材料選型。
相關(guān)鏈接